Hydrogen plant makes Ovako unique in the world
On September 5, 2023, the world's first plant for fossil-free hydrogen for heating steel before rolling was inaugurated. The new plant in Hofors starts a new chapter in Swedish steel history with the potential for major emission reductions.
The plant is now in operation, producing fossil-free hydrogen to fuel our steel heating furnaces and reduce the emissions from our rolling mill to almost zero. As well as being the first electrolysis plant in the world at a steelworks, it’s also Sweden’s largest electrolysis plant, being rated at 20 MW and able to generate 3,880 cubic meters of hydrogen per hour.
Ovako's Hydrogen Plant - lessons in sustainable steelmaking
Looking ahead, the hydrogen plant at Hofors is the first milestone in our roadmap to cut emissions from our mills by 80 percent by 2030. This will see us converting steel heating furnaces at all our rolling mills, provided there is good access to fossil-free electricity or a local source of low-emission hydrogen.
The Hofors hydrogen project started in March 2020 after successful testing of hydrogen fuel with Linde. We then carried out the essential steps of securing investment and gaining approval from the Swedish Energy Agency.
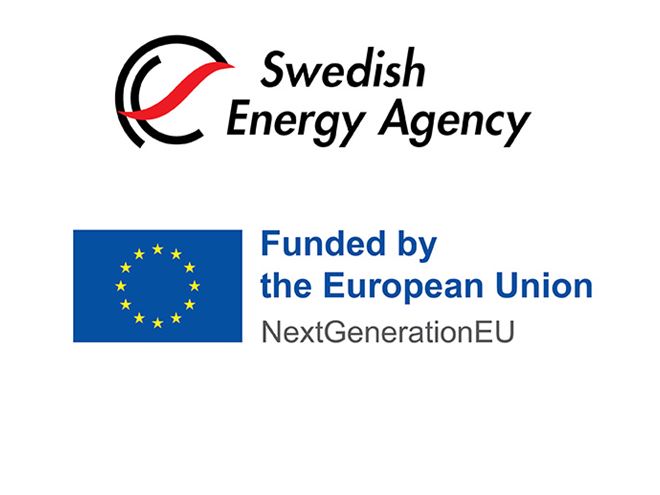
Key partnerships driving fossil-free hydrogen for steel heating
The project is made in partnership with key players in Swedish and Nordic industry such as Volvo Group, Hitachi Energy, H2 Green Steel and Nel Hydrogen. They are supplying Ovako with different components and technical solutions for the plant. The plan is to use local hydrogen production in all Ovako’s units where steel is rolled by 2030, provided there is a good supply of fossil-free electricity.
Why hydrogen is the future of sustainable steel heating?
Steelmaking requires intense heat at three stages in production: melting, hot-forming and heat treatment. We have already converted our melt shops and heat treatment furnaces to zero-emission electricity.
That only leaves the heating furnaces for hot forming processes such as rolling or forging, which operate at 1200 °C. Today’s technology can only achieve this by burning fuel and converting them to hydrogen is the best way to cut emissions for now.
Therefore, producing hydrogen using the alkaline electrolysis process is an indirectly way to electrify the heating furnaces and tackle this area of CO2 emissions.
“Our steel mill in Hofors was founded as early as the 16th century, and with the new hydrogen plant, we begin a new chapter in Swedish steel history. Heating steel products has previously required large amounts of fossil fuels. We are now the first in the world to heat steel with fossil-free hydrogen before rolling, reducing the emissions in this production step to almost zero," says Marcus Hedblom, President and CEO Ovako Group.
It is an investment that was made possible with the support of the Swedish Energy Agency, Energimyndigheten, under the Industrial Leap initiative, as well as the European Union.