Abrasive wear shortens the life of equipment in agriculture, construction, mining and other industries. When a machine experiences excessive wear, it has to come out of service and go for repair or be replaced completely.
Operators want to avoid these costs by using components and materials (like WR-Steel) that have better wear resistance. However, not all wear is the same so there is no “one size fits all” solution.
If you want to minimize wear and tear on your machinery, it’s vital to understand what sort of wear it will experience. That will help you choose the right material to withstand it.
There are four wear mechanisms to understand. All of them happen at the microscopic level and are caused by a hard, rough surface coming into contact with a softer surface under force.

- Plowing happens when an abrasive particle causes the softer material to shift sideways, forming a groove with ridges on either side.
- Cutting is mainly found when abrasive particles impact the surface and act as tiny cutting tools that literally chip away at the surface.
- Wedge formation is a combination of plowing and cutting where pieces of grit burrow into the surface forming wedges that eventually detach.
- Cracking, or brittle fracture, can happen when impacts by the abrasive material create highly concentrated stresses upon impact, leading to the formation of micro-cracks.
How wear mechanisms apply
While it’s good to know the theory, it’s more important to know how these wear mechanisms apply in the field. In our studies we found that these four mechanisms apply differently, depending on the real-world application.
For example, our R&D team analysed equipment from construction, agriculture, drilling and mining. They found extensive micro-plowing and micro-cutting on a Bolt On Edge (BOE) attached to the bucket of a wheel loader vehicle.
We also looked at the tine points that penetrate the soil on agricultural machines like cultivators. Micro-plowing and wedge formation were the most active wear mechanisms here.
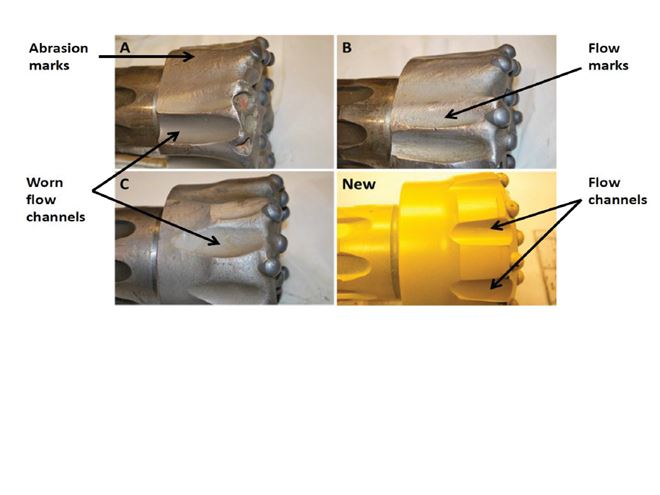
We’ve also studied down-the-hole (DTH) drill bits, which experience impact from airborne particles during drilling. The result is extensive cutting and loss of material, as well as brittle fracture. And while rock tools appear similar to DTH tools, wear applies differently, with evidence of deep plowing on the sides of the tool but cutting and cracking on its top face.
We have done extensive research to help customers identify the wear mechanisms that apply to their equipment and choose a grade of WR-Steel with the right strength, toughness and abrasive resistance to match the application.
For more details, download our Technical Report, Understanding wear mechanisms – the application technology behind WR-Steel.