Last December, for the first time, Ovako Imatra mill started up training for the vocational qualification in process industries focusing on metallurgical industry. In addition to practical experience at the workplace, the apprenticeship trainees will complete four study modules. As in all Ovako operations, the starting point for the apprenticeship training is our key priority – safety.
“A module called ‘Safe work in process industries’ is a natural starting point for apprenticeship training. It is extremely important to make it clear to all new employees right off the bat that safety is our number one priority. The safety training is also a quick way for new employees to get to know the all mill areas,” says Helena Kumpulainen, Ovako Imatra’s HR, Communications and EHS Director.
The apprenticeship training consists of four study modules of roughly four to six months. In addition to safety topics, the training focuses on maintenance, metallurgical processes and metalworking processes. At the same time, the trainees will become familiar with the various work stations of the product unit, including hands-on experience.
“We need new employees who are familiar with our mill on a more general level and are capable of switching between work stations if necessary. Multi-skilled people will enable our production to better respond to varying workloads at our work stations and production lines. Simultaneously, this lets us prepare for upcoming retirements and other types of personnel turnover,” Kumpulainen says.
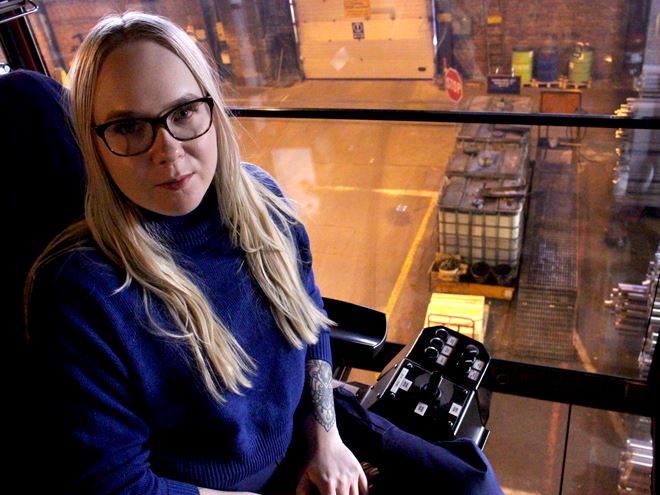
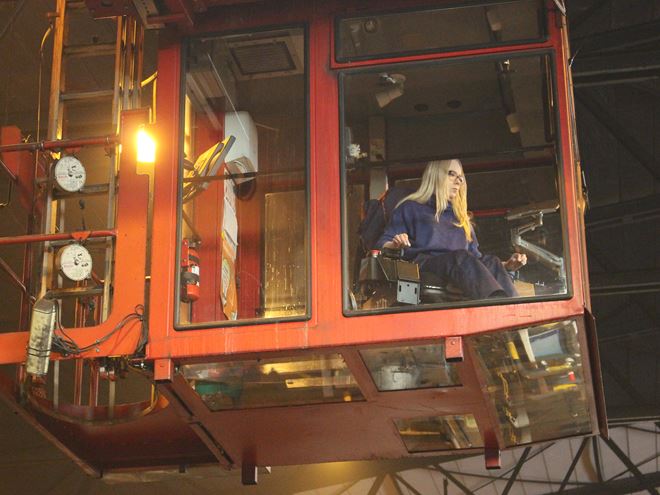
The apprenticeship training is arranged in co-operation with the local Saimaa Vocational College Sampo. The newly started apprenticeship training in something new both for Ovako and Sampo.
“Sampo’s strategy for 2022–2025 states the following mission: We build expertise, wellbeing and vitality. This collaborative apprenticeship training is a prime example of that. It is great to partner with Ovako to train future professionals,” says Mikko Kojo, Sampo’s head of training in electrical engineering and automation technology, processing industry and laboratory technology.
Sampo’s team instructors Harri Rissanen and Annina Lehtonen, who work with Ovako’s trainees, agree with Kojo.
“We are now co-operating with Ovako for the first time, and we are very excited. The trainees are highly motivated and eager to learn.”
One of the new trainees is Tiia Matikainen from Imatra. Friends and family working at Ovako encouraged her to apply for the apprenticeship training. Tiia, who has previously studied vehicle mechanic and worked in construction, is interested in the possibility to gain permanent employment with Ovako.
“After the overall induction, I have started training to use a 12-tonne crane in the further processing department. At first it actually felt a bit scary to sit in the crane cabin, but my instructor was very good and helped me gain confidence. A crane operator needs to work cautiously, and as a calm person, I soon realised that this is just the right job for me. Safety is something that has been highlighted a lot during the training and here in the production unit. Also here when working here with the crane, safety comes first,” Tiia says and starts relocating the next bundle of bars with her crane.