Christoph Gallo, from Ovako’s technical support team in Germany, explains how a switch to IQ-Steel helped the BRS Motorsport racing team boost the transmission performance on its Formula Student car.
Formula Student (FS) is Europe's leading educational engineering competition. It celebrated its 25th anniversary in 2023. With the backing of industry and high-profile engineers, the competition aims to develop enterprising and innovative young engineers and encourage more of them to take up a career in engineering, with over 100 university teams taking part every year.
The project usually forms part of a degree-level project and is viewed by the motorsport industry as the standard for engineering graduates, transitioning them from university to the workplace. During the championship, student teams design, construct and build small formula race cars to compete in international competitions. The competition is divided into static and dynamic disciplines. The winner of the competition is the team which wins the most points across both.
Germany’s BRS team https://brsmotorsport.de/en/, from Hochschule Bonn-Rhein-Sieg, is a seasoned competitor. For its attempt on the 2023 title, it fielded a new design – the G23 “Moni”.
One of the G23’s key refinements was an uprated transmission system that would improve the chassis dynamics by allowing the motors to be moved further into the wheels. At the same time, the 1.5-stage planetary gearbox was replaced by a 1-stage design, increasing the gear ratio from 13.6 to 14.3. This boosted performance within a more compact package, and at the same weight. The previous 1.5 stage setup was also complex to manufacture and demanding to maintain, as well as requiring special tools.
The challenge for the BRS team was that they recognized that the steel they had been using for the planetary and sun gears, 18CrNiMo7-6 (a case hardening steel with high toughness), would be pushed close to its safety margins by the new design. This was due to the higher loadings imposed by the 1-stage gearbox.
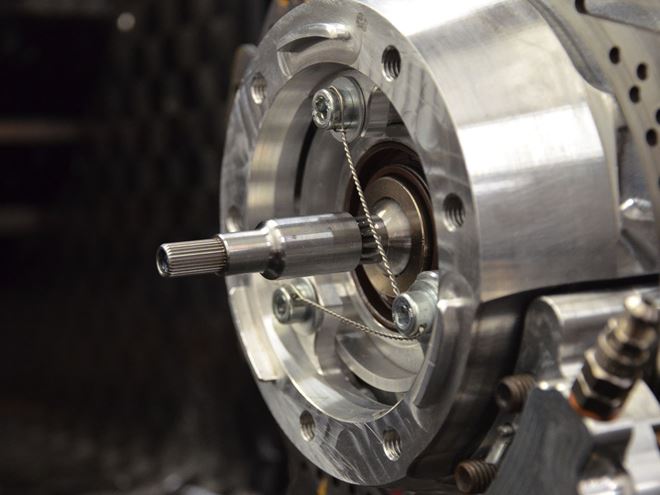
IQ-Steel steps up
The students consulted the specialist gear design software developed by GWJ. This included the web-based software eAssistant, the desktop application TBK and the special software GearEngineer for 5-axis milling of gears. GWJ has incorporated Ovako’s 159Q high-performance clean steel into the software and while exploring the materials options available, the students could see the clear benefit it offered against the standard steel.
159Q is an isotropic quality steel (lQ-Steel®) that is produced with strict control over inclusions so that they are small and spherical. The spherical shape means that the material provides the same consistently high fatigue strength to ensure uniform and excellent properties in all loading directions.
The next step was for the team to engage with Ovako. Together with my colleague Elias Lothman, Senior R&D Engineer at Hofors, we were happy to provide help, advice and sample materials. We were able to confirm that 159Q would be a suitable upgrade.
Building in an increased safety factor
The innovative G23 gearbox, unique in the Formula Student series, features a sun gear and six planetary gears, all manufactured from 159Q. They rotate within a ring gear. This is manufactured from 255G, which is Ovako’s BQ-Steel® (bearing quality) version of 18NiCrMo14-6, a case hardening steel with high toughness used for bearing and transmission components.
The switch to 159Q enabled the safety factor on the gear tooth flank to be increased from the marginal level of 1.037 with the standard steel to 1.373 that provides higher reliability in racing conditions. The new design also delivers increased performance within the same weight package as the old design. This was a crucial element as total weight is often a limiting and decisive factor when designing a racing car.
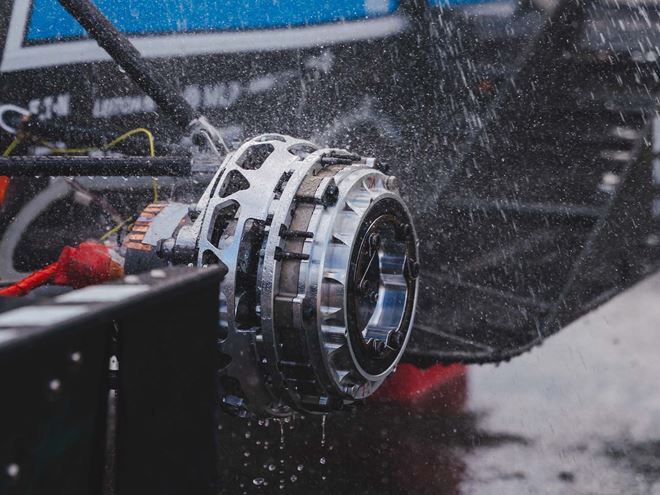
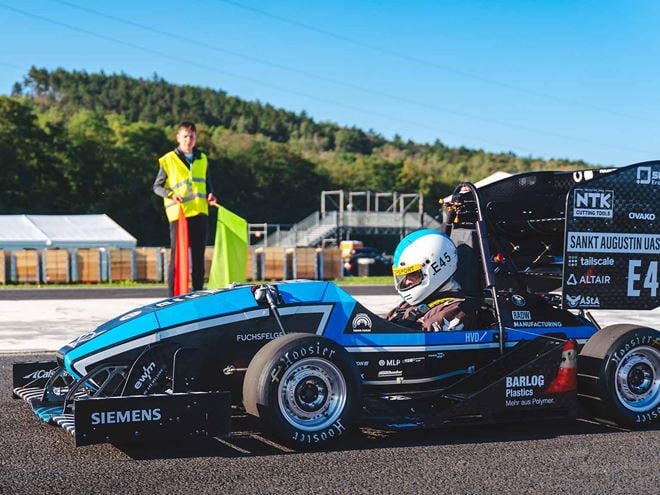
Driven to success
The BRS team fielded the G23, proudly bearing an Ovako logo, at two Formula Student events during 2023, in Italy and the Czech Republic. It was at the second outing where the team enjoyed its greatest success, with second place in the Cost and Manufacturing category followed by First place in Engineering Design. That made it a trio of wins in this category following previous triumphs in Italy in 2016 and Spain in 2021.
Catching the minds of future engineers
At Ovako we love working with student teams like BRS, because it enables us to capture their minds at the very start of their career to educate them on the performance benefits of clean steels. This is important as many of these students will go on to have careers in the automotive industry. And of course, their experiences provide us with useful case studies.
Furthermore, both Elias and I as the primary contacts for the student teams have gained a lot of insights by participating in the technical discussions about their drivetrain concepts. We find that they experience the same basic challenges as the major automotive OEMs – just on a smaller scale. Hence, our dream scenario is to be able to transfer these small case studies in racing into substantial industrial applications.