What steps are you taking to reduce emissions from heating before rolling?
Throughout history, burning fossil fuels, such as to heat steel before rolling, has been an integral part of the production process. And of course, the resulting CO2 emissions are a very significant element in the carbon footprint of steel products.
In September 2023, we inaugurated the world's first plant for fossil-free hydrogen for heating steel before rolling at our Hofors plant in Sweden. This has helped to reduce emissions from the rolling mill to almost zero. As well as being the world’s first electrolysis plant installed at a steelworks, it’s also Sweden’s largest electrolysis plant, being rated at 20 MW and able to generate 3,880 cubic meters of hydrogen per hour. Ultimately, we plan to convert the steel heating furnaces at all our rolling mills to fossil-free energy sources.
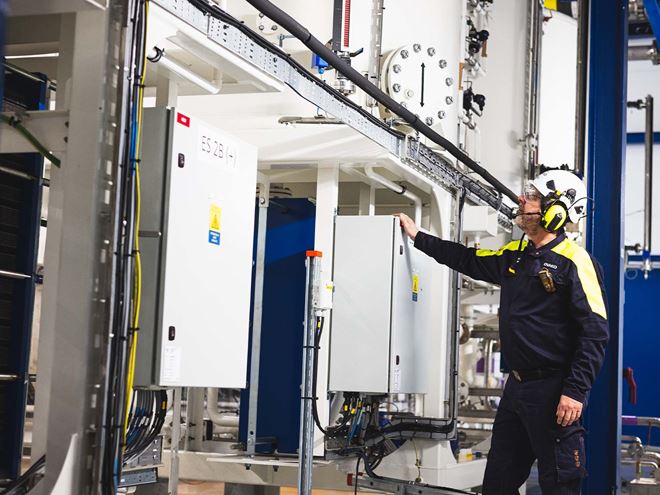
Do you use fossil-free electricity?
The steel industry is a heavy user of electricity, especially in electric arc furnaces (EAFs). Switching from electricity generated by burning fossil-fuels to renewable energy from hydropower, wind or solar sources can enable a tremendous reduction in carbon emissions.
This is we use 100% fossil-free electricity in our steel and rolling mills. This is made possible through the energy mix contracted with our electricity supplier. This results in close to zero emissions from the electricity we purchase, which comes under Scope 2 accounting).
In the past 5 years, 88% of Ovako's residual products have been recycled
How do you fuel your heat treatment processes?
Heat treatment is a vital step in achieving the desired final properties of steel products. But, heat treatment furnaces that are normally fuelled by gas, produce CO2 emissions. Converting them to electric heating is another important step to a carbon neutral steel industry.
At Ovako we have adopted a major initiative to convert our heat treatment furnaces to electricity. So now 90% of the heat treatment we carry out is with electric power.
Have you optimized your use of recycled content?
Steel is the world’s most recycled material. It can be remelted again and again without affecting its properties. It takes much less energy to recycle existing materials than it does to process virgin raw materials. That means reusing existing resources is a good way to reduce CO2 emissions – especially in steelmaking where it is possible to reduce emissions by over 80% using scrap-based steel.
Estimates suggest that by volume, scrap will account for 50% of the global iron content in steel by 2030, up from 35% today. At Ovako we are already ahead of the game, since our steel currently contains 97% recycled content, making our products almost completely circular.
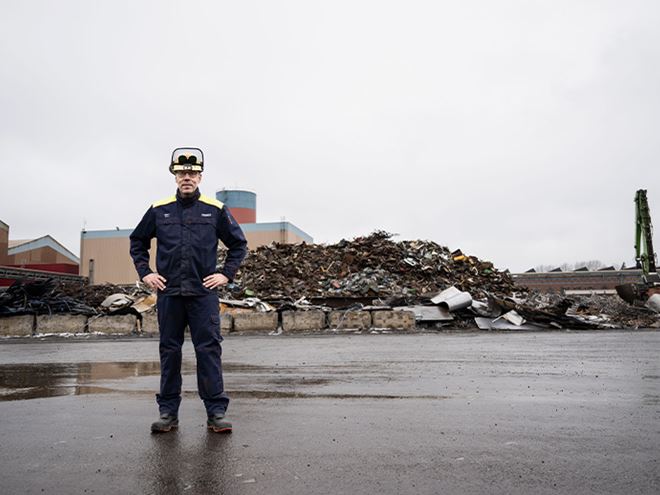
Can you provide product carbon footprint calculations for your delivered products covering all three scopes?
To gain a full picture of the carbon footprint of a steel product there are three Scopes that must be considered. Scope 1 emissions are the greenhouse gases that an organization emits from sources it owns or controls directly. Scope 2 emissions are indirect, deriving from an organization’s purchase of electricity, steam, heat, or cooling. Scope 3 emissions cover indirect emissions from feedstock material, energy and the like used in the steel production, as well as transportation.
Because Scopes 1 and 2 are relatively easy to calculate, that is where some steel suppliers stop. However, at Ovako we are committed to also providing Scope 3 information on our delivered products.
This is illustrated by our Carbon Calculator tool. This builds upon our Environmental Product Declarations (EPD®). These are verified and registered documents that provide transparent and comparable information about the environmental impact of products over their life cycle. In the Carbon Calculator, we combine data from our EPDs with activity data for all our different process routes and steel grades, enabling us to provide specific carbon footprint calculations on all product deliveries.
This information helps customers to make accurate carbon footprint calculations on their products, and informed decisions about their steel purchases.