Ovako is now able to combine the advantages of forging and rolling processes to produce black bar at outer diameters up to 230 mm. Jimmy Gran, VP and Head of Product Unit Black Bar - Ovako BU Hofors- Hellefors, explains the benefits of the new production flow.
How the black bar is formed
Black bar, formed by hot rolling, is usually manufactured in diameters up to 160 mm. Beyond that size it becomes technically challenging to produce a high-quality product. But we have seen a growing demand for black bar in larger diameters. This has come from customers manufacturing critical components for bearing and mining applications. That is why we decided to explore the possibilities of a new production flow with the bar being forged before rolling to its final size.
We roll black bar at a temperature of 1200°C. Because this is well above the steel’s recrystallization temperature, typically 400 to 700°C, the bar is malleable and easy to form. However, the porosity in the steel from the casting process means we cannot go above a diameter greater than 160 mm if we want to achieve an internally-sound high-quality rolled product.
Through hot forging we achieve a consolidated and sounder internal structure. But it is a relatively expensive way of producing bar in dimensions up to 230 mm, especially as it is sometimes necessary to carry out time-consuming additional forging and reheating operations. Furthermore, the surface quality and dimensional tolerances of a forged bar are usually inferior to a rolled bar.
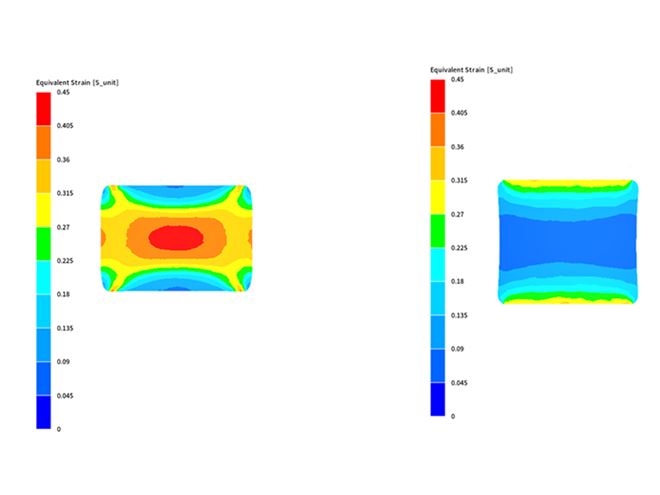
Most grades can be forged-rolled
We can apply the forged-rolling process to most of our steel grades. It is also suitable for use with our clean, bearing-quality, BQ-Steel. This steel has been established for decades as a problem-solver in the bearing industry thanks to its dramatically increased fatigue strength.
Confirming the internal soundness of black bar
Achieving consistent quality is vital for the success of our new forged-rolled product. That is why we placed a major focus on developing testing techniques to verify the internal soundness of the bar. This includes the use of the phased-array ultrasonic test equipment shown in Figure 3 to monitor the entire production output.
Extensive trials have demonstrated that through the forged-rolled process we achieve a level of soundness that is significantly better than rolling alone. The results are also comparable with a bar processed entirely by forging.
Figure 4 shows the ultrasonic examination of a 230 mm diameter bar manufactured in 837R. This through-hardening bearing steel is used mainly for medium-sized bearing rings. However, it can also be used for machine components that require high tensile strength and high hardness. The R designation shows that it is a bearing quality (BQ) variant.
The testing was performed from bottom to top along the whole length of the billet. It was calibrated against a 2 mm flat-bottomed hole (FBH) as shown by the horizontal red line on the scan.
To examine the results further, we subjected samples from the bottom and top of the bar to immersed ultrasonic inspection. This time the calibration was with a 0.2 mm FBH. Figure 5 shows the clear improvement in the level of porosity with the pre-forged route.
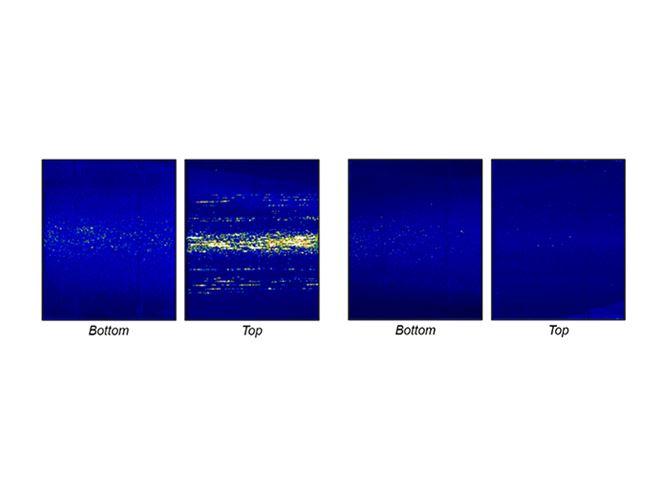
Forged-rolled bar is ready to roll out
We are seeing a great deal of interest in our forged-rolled bar, especially from customers in the bearing and mining industries, and several test orders have already been completed. Approvals are in place for some of the most popular steel grades, and eventually these will be extended to cover most of Ovako’s portfolio. All the equipment is up and running smoothly ready for volume production.
The simulations of forging and rolling shown in Figures 1 and 2 indicate the differences that the two operations have on the internal strain in the bar.
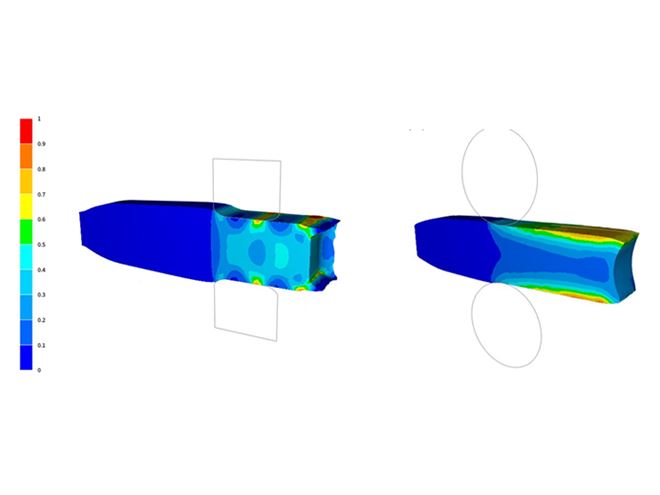
Bringing the best of both worlds
To tackle the challenge of producing black bar in the increased sizes demanded by customers our R&D and production teams collaborated to establish a new forged-rolled production flow. It starts by putting the cast steel ingot through a multi-pass forging operation. This consolidates the internal porosity and produces a billet of an intermediate size suitable for rolling.
We then hot roll the billet to the final required dimension. The result is black bar with both a good surface finish and dimensional accuracy. This reduces the need for our end-customers to carry out final machining.
Our Hofors and Hällefors sites were selected for the new production flow as they already had forging and rolling processes in operation. To bring them together we have made major investments in handling equipment such as manipulators and overhead cranes.
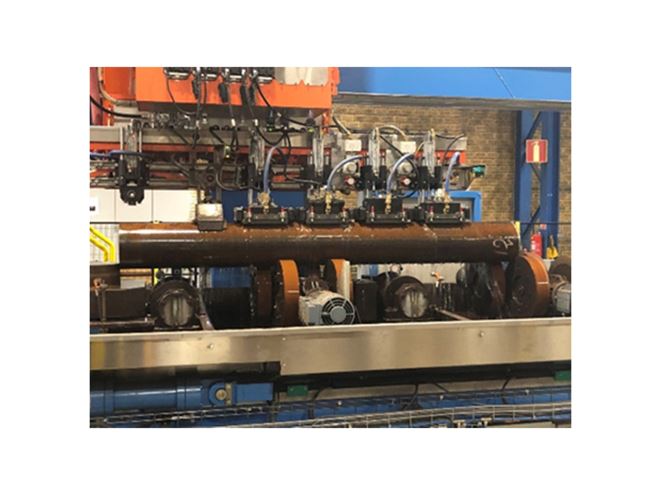
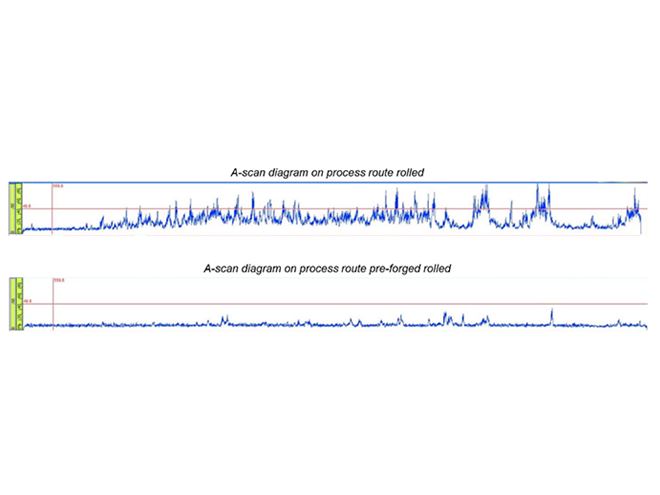
We also carried out microscopic examinations on production bars rolled to a diameter of 190 mm, with samples taken from the bottom, middle and top of the billet. The steel grade for this test was 827B, similar to the 837R examined in the ultrasonic tests. Figure 6 shows the good correlation with the ultrasonic testing, confirming that the forged-rolled process offers a significant reduction in porosity.
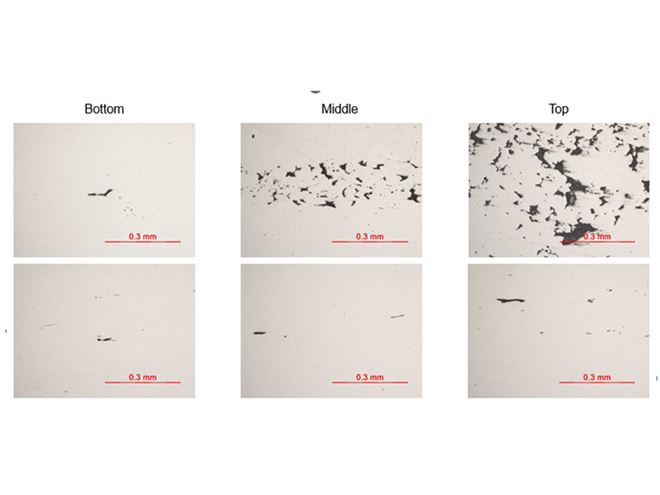