In September 2023, Ulf Kristersson, the Swedish prime minister came to Ovako’s Hofors mill for the official inauguration of the world´s first fossil-free hydrogen plant for heating steel before rolling. Anders Lugnet, Ovako’s Technical Specialist, Energy-& Furnace Technology, explains how this development offers significant potential for global emissions reduction.
We are now producing hydrogen at Hofors with a new electrolyzer plant that will enable us to cut our CO2 emissions by 20,000 tonnes per year by reducing Ovako’s reliance on fossil fuels. As one of the largest electrolyzers in Europe, the 20-megawatt (MW) plant will generate 3,880 cubic meters of fossil-free hydrogen per hour, as well as producing oxygen.
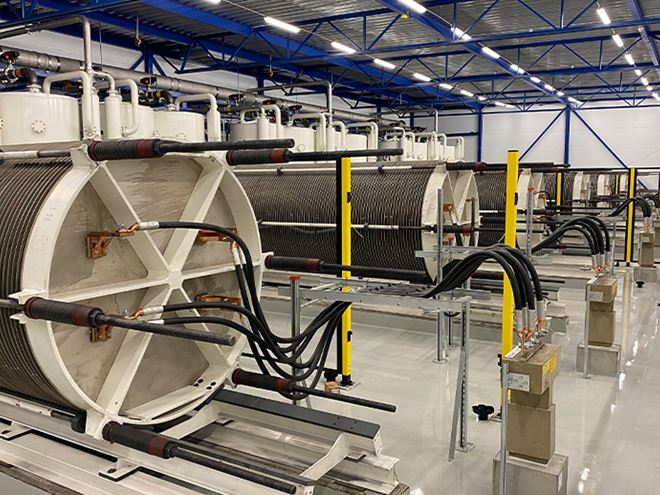
The electrolyzer is just the latest milestone along the path towards our long-term goal for zero-emission steel production. The origins of the Hofors steel mill date back to the start of iron production in 1549. In more recent times, we made our first step into sustainability in 1930 with our first electric arc furnace (EAF). Major steps since then include closing our last blast furnace in 1977, conversion of steel heating furnaces to oxyfuel in 1995, starting electrification of heat treatment furnaces in 2012 and publishing our first verified climate declarations in 2018.
Looking ahead, electrification is essential for the next steps in our decarbonization journey. Steelmaking requires intense heat at three stages in production: melting, hot-forming and heat treatment. We have already converted our melt shops and heat treatment furnaces to zero-emission electricity.
That only leaves the heating furnaces for hot-forming processes such as rolling or forging, which operate at 1200°C. Today’s technology can only achieve this by burning fuel and converting them to hydrogen is the best way to cut emissions for now.
Therefore, producing hydrogen using the alkaline electrolysis process is an indirect way to electrify the heating furnaces and tackle this area of CO2 emissions. This is where our new hydrogen plant comes in. It draws on low-carbon Nordic electricity to produce low-emission hydrogen to fuel the reheating furnaces at Hofors.
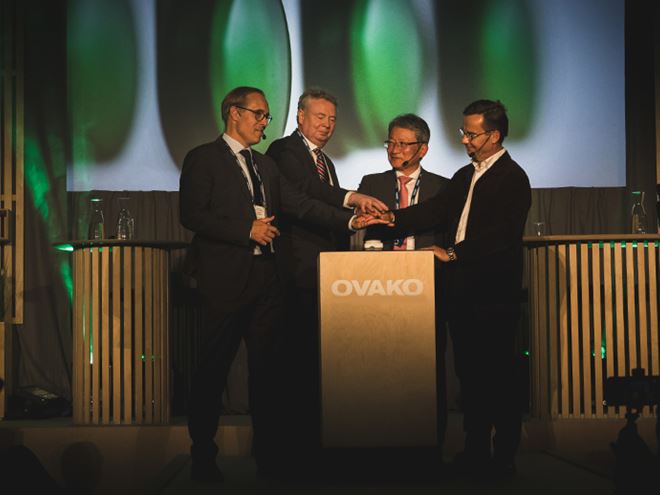
Trial lays the foundation for hydrogen conversion
The decision to switch to hydrogen was based on a project with Linde Gas AB in which we completed the world’s first successful full-scale trial in a production environment of using hydrogen to heat steel before rolling. The use of hydrogen in combustion has a great positive effect on the environment since the only emission generated is water vapor.
The trial, in which steel was heated using hydrogen instead of LPG (liquefied petroleum gas) before rolling at the mill in Hofors showed that heating with hydrogen does not affect the quality of the product. This showed that, given the right conditions, Ovako could introduce hydrogen heating for furnaces at all our rolling mills and thereby drastically reduce our already world-leading low carbon footprint from cradle to gate.
Borrowing water
Because the electrolyzer is located close to the furnaces at Hofors, our approach to hydrogen can be seen as borrowing water for a short period of time. The plant draws water from the local supply and splits it into hydrogen and oxygen. Shortly afterwards, we then combine the H2 and O2 into oxyfuel for injection into the furnace, where combustion re-forms water. This approach requires only a few minutes of storage as a buffer for fluctuations in production and demand.
There are a lot of individual components in the system. These include the electrolyzer itself, as well as scrubbers, storage tanks, compressors and pipework, plus electrical transformers and rectifiers, and integration of control and automation systems. Before it came online there was a major phase of shaking down the new plant and performing trials to ensure that system components worked as expected.
Wider benefits
The success of this project has only been possible with financial and technology support from our partners.
Sweden’s Energy Agency provided funding under its Industrial decarbonization initiative. This included support from the EU’s Recovery and Resilience Facility (RRF), which is an element of the NextGeneration EU scheme that is contributing to a more environmentally friendly EU.
From a technology and project delivery perspective, Hitachi Energy and Nel Hydrogen have provided know-how to deliver a plant optimized to fuel our furnaces and also support the stability of the electric power grid.
Our other partners are Volvo Group and H2 Green Steel. They are important for the wider adoption of hydrogen. Volvo will use experience at Hofors to inform its “cellcentric” joint venture with Daimler Trucks that is evaluating the potential use of hydrogen as a fuel for emission-free road transport. Similarly, H2 Green Steel will use our experience as a legacy steelmaker in deploying hydrogen technology to inform its greenfield approach to low-emission steelmaking.
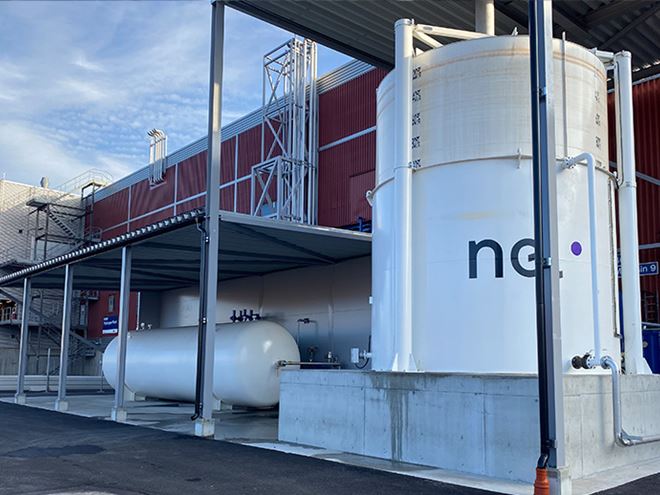
Looking forward
Our plan is to use local hydrogen production in all Ovako units where steel is rolled by 2030, provided there is good access to fossil-free electricity to power the electrolysis process.
Read more about Ovako’s path to carbon neutrality
Read the latest issue of Bergsmannen 'Nordic Steel & Mining Review'