Thomas Björk, PhD, Group Technical Specialist, Ovako Sweden AB, outlines a recent research program that shows both recycled steel and ore-based steel are equally good as raw materials for automotive crankshafts.
Historically, a number of automotive industry OEMs have been reluctant to use recycled steel for their crankshafts. This is despite its considerable potential to reduce the carbon footprint of their products. The reason is an historic belief that engine crankshafts should be manufactured from ore-based steel, mainly because it performs better during the grinding operations necessary to create high-quality bearing surfaces. Recycled steel is considered by some to be more susceptible to “grinding burns”. This is a type of thermal damage that decreases surface hardness, introduces tensile residual stress and shortens fatigue life.
A number of major players in the industry decided it was time to challenge this by carrying out a test program to benchmark the performance of recycled and ore-based steels. With financial support from the Swedish government, a three-year project was devised - Grindability of recycled steel: automotive crankshafts (CRANK-STEEL). It was coordinated by Chalmers University of Technology, with project members including Volvo Group, Volvo Cars, Scania, Bharat Forge, Ovako and RISE IVF.
How to assess the grindability of a material?
The first challenge for the project was in how to assess the grindability of steel. This is because there is no grinding-specific definition. It was therefore decided to use the general concept of “machinability”. This describes the ease with which a certain material can be machined under given process conditions and it may be assessed by one or more of the criteria:
- Tool life & tool wear
- Material removal rate (MRR)
- Cutting force
- Surface finish
- Chip shape
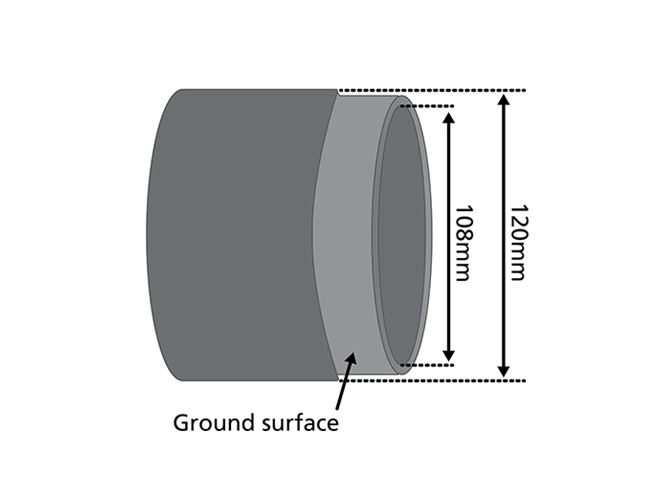
Figure 1 – The workpiece used for the grinding tests.
Grinding tests
To carry out the tests, tubular, hardened workpieces (see Figure 1) were fabricated from bars in a steel grade used regularly for forging. These were divided into two groups from different steel makers:
- Steel production based on recycled material
- Virgin ore-based steel
These two materials are nominally identical. However, some small differences were observed that influenced the test results, even though they remained within the specified parameters.
The test pieces were hardened by austenitization at 870°C for 1 hour followed by water quenching and tempering. Three main indicators were used to assess the grindability of the two materials:
- Specific energy - Is there a difference in energy required to grind the materials?
- Wheel wear - Is there a difference in how the grinding wheel wears down?
- Surface integrity - Are there differences in the surface integrity of the ground surfaces?
The tests were carried out using a grinding machine. They comprised cylindrical plunge grinding with 1/3 of wheel width:
- Grinding 3 mm off the radius in a single pass
- 16 plunges in total per material (with decreasing infeed)
- 3 measurements of the wheel profile for each test piece – at the start, halfway point, and at the end
Specific energy
The specific energy used during the tests was calculated as shown in Figure 2. This shows that the specific energy required to grind both the test materials was broadly similar.
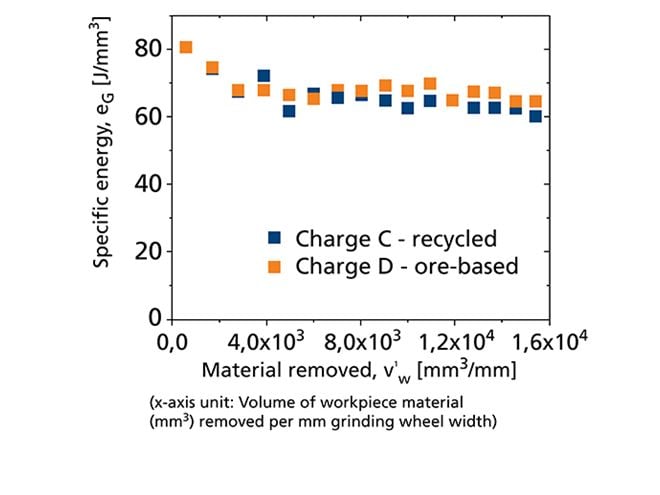
Figure 2 – Results of specific energy calculations.
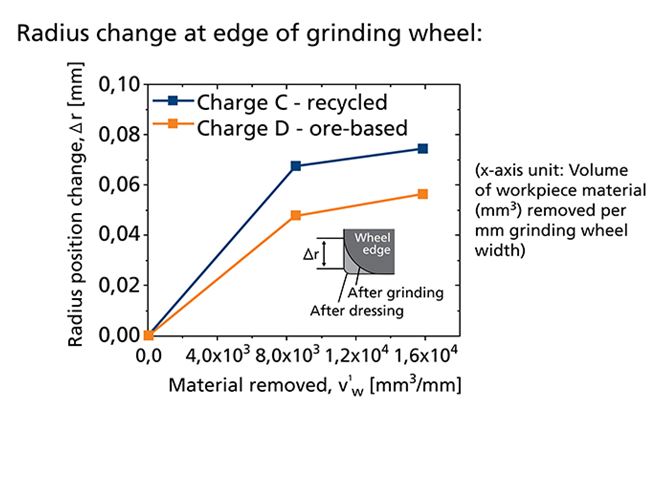
Figure 3 – Wheel wear tests.
Wheel wear
Wheel wear was assessed by measuring geometrical changes in the grinding wheel as increased amounts of steel were ground away. This is shown in Figure 3.
It is clear that there is a larger radius change and hence wear for grinding recycled material. However it should be noted that the observed changes in the radius are smaller than the CBN grit size (181 µm grit diameter).
There could be a number of possible reasons for the different wheel wear rates. Clearly, the mechanical and thermal loads on both materials are similar – as indicated by the similar specific grinding energies and residual stress profiles (see next section). Therefore it is most likely that hard non-metallic inclusions influenced wheel wear. This was confirmed by metallurgical tests that showed a slightly higher proportion of both soft magnesium sulfide (MnS) inclusions as well as hard aluminium rich oxides in this particular batch of recycled steel.
Surface integrity tests
The surface integrity tests were carried out using the same grinding parameters as the wheel wear tests. However, the workpieces were switched from time to time to focus on the effect of the workpiece material and exclude the potential effect of changing wheel topography.
Surface integrity was assessed using Barkhausen Noise (BN) measurement. This is a non-destructive method involving the measurement of a noise-like signal induced in a ferromagnetic material by an applied magnetic field. There are two main material characteristics that will directly affect the intensity of the Barkhausen noise signal: hardness and stress.
An increase in BN is usually connected to more tensile residual stresses and/or decrease in hardness (tempering) – the result of grinding burns. In contrast, a low BN is associated with compressive residual stresses and/or high hardness.
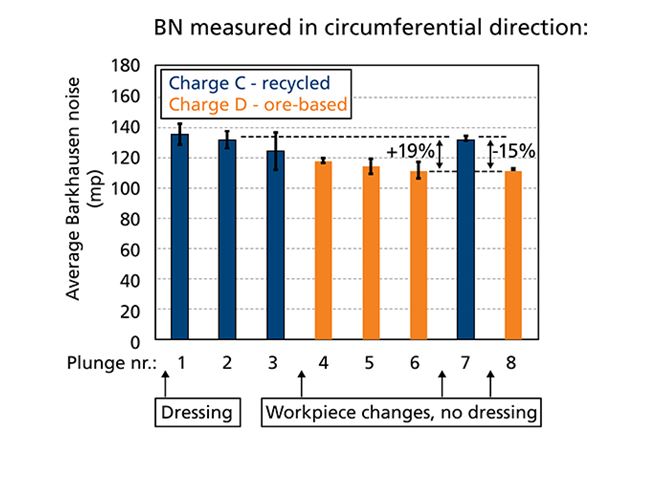
Figure 4 – Results of Barkhousen noise (BN) analysis on ground surfaces.
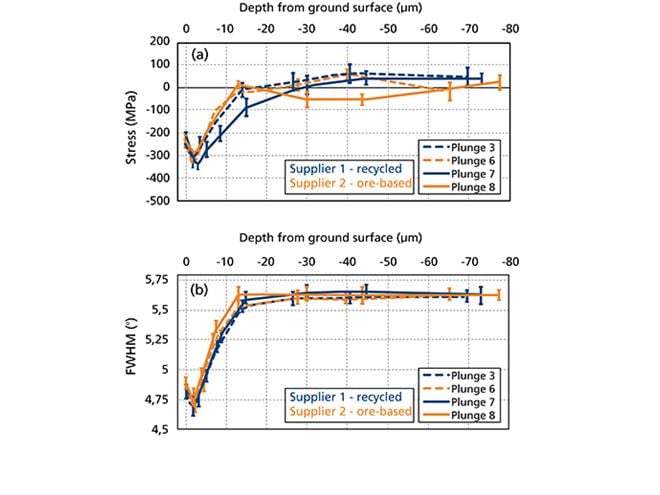
Figure 5 – X-ray diffraction measurement of residual surface stress.
The results shown in Figure 4 show a clear difference between the recycled and ore-based steels, indicating different surface integrities and suggesting worse grindability of recycled material.
To investigate further, X-ray diffraction measurement of surface residual stress was carried out – with the results shown in Figure 5. These did not confirm the indications given by BN and the stress profiles are very similar for almost all measurements.
Full width half maximum (FWHM) values, as shown in the lower part of Figure 5, are an indication for the surface hardness and deformation of the material. The plot shows that there are no differences between the materials and plunges, suggesting that similar surface hardness and deformation is present in both materials.
Further investigation was carried out since it has been reported that - apart from residual stresses and hardness - BN is affected by material microstructure. The microstructures of the two materials were therefore compared.
The tests showed a slightly lower bulk hardness for the recycled batch and similar martensite morphologies for both materials. However, there was a difference in the average size of the prior austenite grains – these were larger in the recycled steel and studies report that larger grains result in higher BN. The reason for this difference is believed to be varying amounts of carbon nitrides when the materials were austenitized, which resulted in different grain growth rates.
As a next step, BN measurements were performed on metallographic samples taken from the workpieces. The goal was to minimize the influence of surface deformation/stresses and instead measure the bulk material’s BN response. The results show, as in the grinding tests, a higher BN for the recycled steel batch. The conclusion is that the increased BN level is an artifact of grain size rather than resulting from the grinding process.
Summary and conclusions
The test program has enabled a number of conclusions to be drawn:
- When considering the likelihood of grinding burn occurring, when using dedicated CBN wheels to grind automative crankshafts, the steel sources, whether from recycled steel or ore- based steel, are equally good.
- Among the grindability measures, wheel wear was seen to be higher for the recycled steel as compared with the ore-based batch. The reasons for varying wheel wear and grain size differences are due to micro-constituents in the materials (inclusions and carbon nitrides) and not related to macro-properties such as hardness.
- Barkhausen noise analysis appears to be sensitive to microstructure, especially grain size. This can lead to possible misinterpretation of increased BN levels of a ground surface as thermal damage. To avoid this, an unground reference sample from the relevant steel supplier should be used to calibrate the parameters for the Barkhausen test equipment.
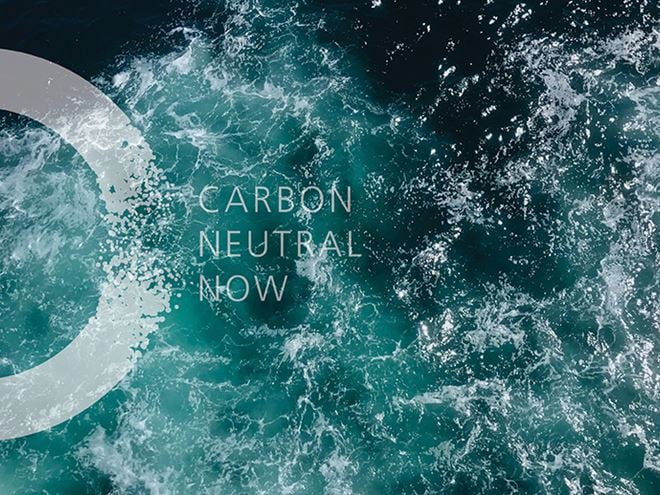
Implications of the grinding test program
For automotive OEMs, the positive results of this test program will help remove the barriers to using recycled steel. The implications for sustainability could be significant. It is hard to put an exact figure on how much steel is used each year in the manufacture of crankshafts. But we do know that some 90 million internal combustion engine vehicles are produced each year. Therefore a conservative estimate is that the annual use of steel for crankshafts is in the order of several million tonnes, most of it currently ore-based.
The carbon footprint of ore-based hot-rolled bar is well over 3,000 kg of carbon dioxide (CO2) per tonne, as illustrated in the Ovako white paper “Cradle-to-gate – understanding CO2 footprint of hot-rolled bar steel products”. (PDF file). In contrast, one tonne of our bar steel from the Smebox mills generates just 389 kg of CO2. Other suppliers may have have higher values. Even so, an industry-wide switch to recycled steel for crankshafts could save millions of tonnes of CO2 a year.
From the start of 2022, Ovako is offering carbon neutral steel, made possible by the purchase of carbon offsets. This is an interim step as we progress to fully carbon-neutral production. This offers a further opportunity for automotive OEMs to drive down their carbon footprint. Read more about Ovako’s path to carbon neutrality.