Lessons from the EU’s ETS in tackling climate change and reducing CO2 emissions
“Society is making major progress to cut the greenhouse gases that influence climate change. This is thanks to legislation that dates back some 20 years such as the EU’s Emissions Trading Scheme (ETS),” says Marcus Hedblom, President & CEO of Ovako. “Although it was initially questioned, it’s now clear that the ETS system has been a key driver for a global change in energy strategy over the long term, by starting to put a price on CO2 emissions.”
Today, we’re facing a similar challenge with circularity, how to promote and incentivise an increasing level of circularity in our society. To protect natural resources, there needs to be a clearly understood value in recovering and reusing our raw materials. This will establish the sound business logic for wider adoption of circularity.
It’s possible that the journey will require 5, 10 or 15 years for industry to adjust, making it all the more important to start the transformation now. Progress will require growth in demand for circularity from customers, as well as transparency within the supply chains. But the end goal is a better world.
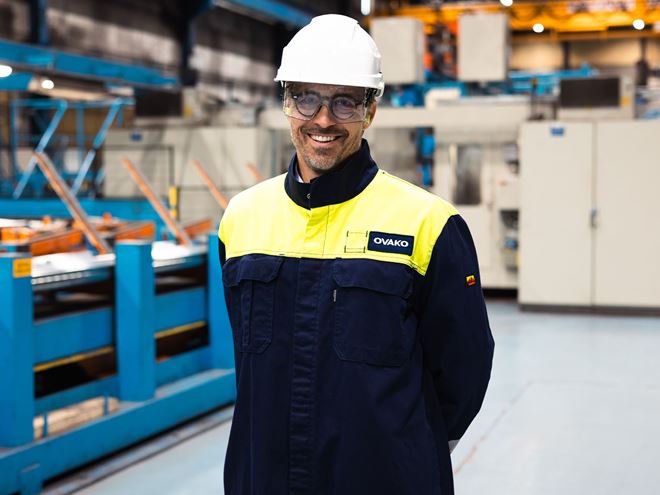
Our products are made from 97% recycled steel, with over 99% recycled content for iron. By recycling both our own and external steel scrap, we conserve energy, reduce emissions, and minimize the use of natural resources. This approach not only prevents valuable materials from ending up in landfills but also positions us as a key player in the circular economy.
We calculate recycled content per European standards EN45557 and ISO14021, including post-consumer scrap, scrap from other industries, shavings, and return steel, while excluding home scrap-scrap generated up to finished ingots or billets. Alloys are the main materials not counted as recycled. This methodology ensures a consistent approach to assessing recycled material in our products.
Ovako ranks among the largest recyclers in the Nordic region. Recognizing that not all steel scrap is the same, we collaborate with long-term, trusted suppliers for our external steel scrap. Once it arrives, the scrap is meticulously sorted into various categories based on factors such as alloy content, size, and shape.
By aligning the scrap’s quality closely with the required steel grade, we’re able to significantly reduce the need for virgin alloys. This approach is a key reason we achieve a “cradle-to-gate” carbon footprint that is 80% lower than the global average.
Ovako’s approach to circularity maximizing recycled steel to reduce co2 emissions and drive sustainability
At Ovako, our approach to circularity focuses on recycling. As noted earlier, our steel already contains 97% recycled content, making our products almost completely circular. Although it could be said that we use steel scrap as a raw material, we prefer to refer to it as recycled steel – a vital input for producing climate-efficient steel in today’s world.
It takes much less energy to recycle existing materials than it does to process virgin raw materials, so reusing existing resources is also a good way to reduce CO2 emissions. In steelmaking, it’s possible to reduce emissions by over 80% by doing this.
The key to maximizing the value from recycled materials is to protect quality through sorting. We have over 15 separate streams of steel for recycling. Each of these has different alloying content and other attributes, making it suitable for remelting into various steel grades.
Efficient recycling is an approach that we’ve worked hard to develop together with suppliers and customers over many years. This was a topic at the Underhållsmässan trade show in Gothenburg, Sweden, where Ovako took part in a panel discussion with SKF and Stena Recycling about how our companies work together to achieve both high business and environmental value through circularity.
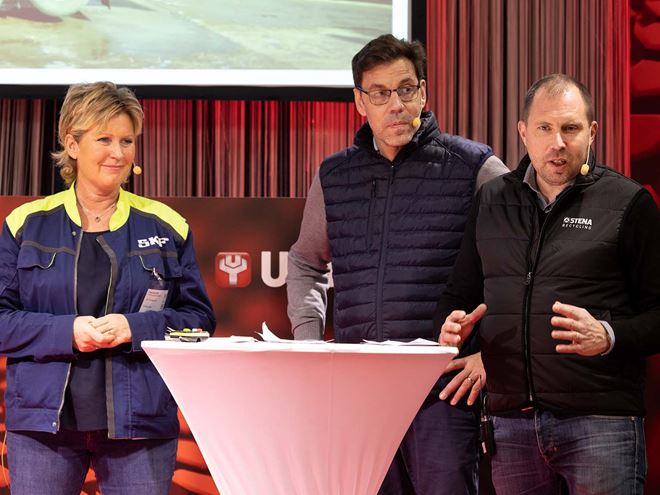