Hybrid Steel®: Superior High-Temperature Strength with Unique Corrosion Resistance
Our Hybrid Steel®, developed for superior strength, especially in high temperature applications, comes with an important bonus in the form of good corrosion and oxidation resistance. But there is a challenge. While it performs much like stainless steel, its significant aluminum content means that it does not conform with the usual PREN (pitting resistance equivalent number) index that predicts corrosion resistance. However, our recent research program has come up with a new approach. Steve Ooi, Ovako Group Technical Specialist, based at Cambridge University, explains.
Steels for high‐performance bearings, fuel injectors for engines and other highly stressed mechanical components require a combination of good mechanical properties and other characteristics. These include high strength, high surface hardness, low inclusion levels, and the ability to be manufactured to high precision with a good surface finish.
Corrosion resistance is also important in applications where potentially corrosive fluids can seep past seals and lubricants. In these conditions it is possible to apply surface treatments and coatings. But this may increase product costs and create recycling problems. The typical causes of corrosion in bearings include condensation, water ingress into the lubricant and acid formation due to lubricant decomposition.
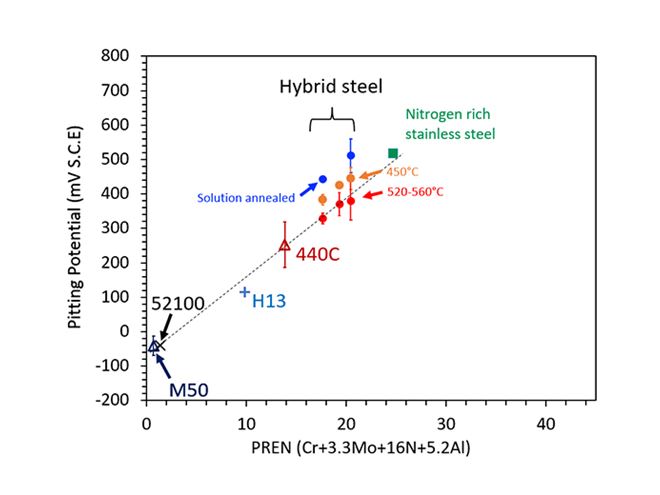
Figure 1. Anodic potential measured in electrochemical tests is a useful indication of the corrosion resistance of steel. Plotting the value obtained for various grades against the new established corrosion resistance index (CRI) clearly demonstrates the benefit of aluminium as an alloying element.
Stainless steels can experience challenges in bearing applications
It is possible to use traditional stainless steels containing around 10.5% chromium (Cr) in bearing applications. Although they do come with some challenges associated with ensuring a satisfactory fatigue life, while increased vibration can also be an issue.
This has prompted interest in using Ovako’s Hybrid Steel that merges the unique properties of high-performance engineering steel, tool steel, maraging steel, and stainless steel. The result is a single high-performance steel grade with the production economy of conventional engineering steel. And while it has a much lower chromium content, tests have confirmed that alloying with aluminum gives Hybrid Steel corrosion resistance that compares well with lower- end stainless steels.
Why PREN isn’t the answer
Traditional stainless steels and their associated production technologies rely on the knowledge that chromium, molybdenum (Mb) and nitrogen (N) alloying help to improve corrosion resistance. To predict how a particular alloy will perform, the percentage composition of each element is commonly translated into the PREN. Pitting corrosion happens when there is a localized breakdown of the protective passive layer on the metal surface. It can eventually result in deep cavities that affect the performance of the component and ultimately cause failure.
There are several formulas for calculating the PREN. But the two most common are:
PREN = Cr + 3.3Mo + 16N and PREN = Cr + 3.3Mo + 30N, where Cr, Mo, and N are chromium, molybdenum, and nitrogen concentration in percentage by weight. Furthermore, both N and Mo are beneficial only when Cr is present.
Partial replacement of chromium with aluminum (Al) or a combined addition of both chromium and aluminum – as in Hybrid Steel - have been shown to enhance the corrosion resistance of steel in certain environments. And in some cases, the alloy achieves a comparable corrosion resistance with conventional stainless steel. However, because Hybrid Steel contains only 5% Cr, together with 2% Al, the existing PREN formulae cannot be used predictively to improve alloy design for corrosion resistance.
Therefore we directed our research at finding a modified formula for a new corrosion resistance index (CRI). Through a literature search we found a related patent by Katoh and Saitoh. This provided the foundation for a laboratory test program, in which we subjected a range of commercial alloys including stainless steels and Hybrid 50, 55, 60, as well as test alloys, to a series of corrosion tests in different environments.
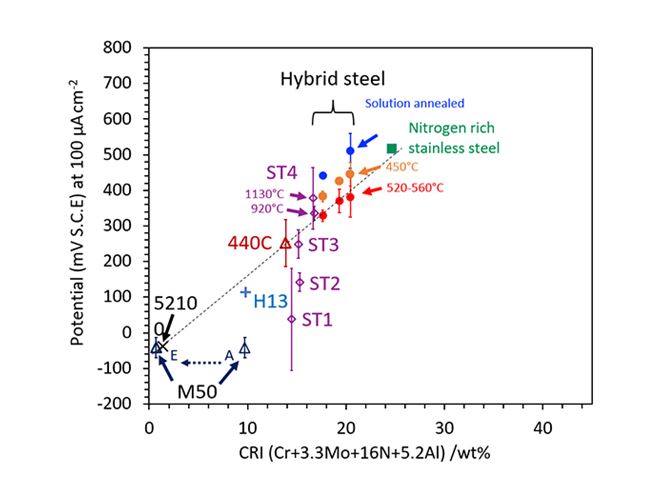
Figure 2: A series of experimental alloys was designed to validate the newly established corrosion resistance index (CRI). This work further validates the positive effect of aluminium in the newly established corrosion resistance index, but also shows that for this index to remain valid, a minimum chromium addition of 4 wt% is needed.
A simple alloy design guide
Our findings were that aluminum enhances the corrosion resistance of chromium‐containing steel with a coefficient of 5.2. That enabled us to create a new formula:
CRI = Cr + 3.3Mo + 16N + 5.2Al.
There are some factors that must be considered when using this formula. Because further study of the experimental alloys showed that for it to be valid, the Cr content needs to be higher than 4% by weight. The atomic ratio of Cr to Al also needs to be higher than 1. Furthermore, this CRI can only be applied in a low chloride (Cl-) environment. This is because an increase in Cl- (as in seawater) reduces the effectiveness of the Al-containing protective oxide film on the surface in preventing corrosion.
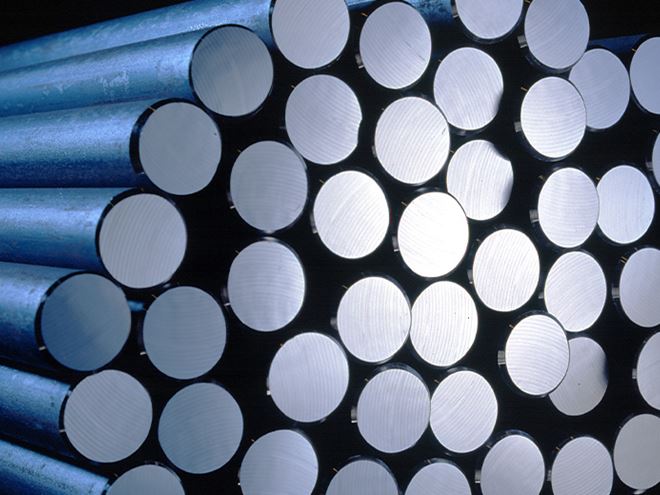