Wrecking bars are invaluable tools for prying apart objects and pulling out nails. Yet, despite its sturdy appearance, a poor-quality bar made from inferior material can snap unexpectedly under pressure, putting workers at risk. That’s why Hultafors, the Swedish hand tool maker, uses high-strength Ovako boron steel for its best quality wrecking bars. The benefit is not only in increased safety, it also enables Hultafors to produce wrecking bars with claws that are thin for great access but still really strong.
A wrecking bar features a claw with a slot for prying up nails, a rounded heel to help drive the claw into position, a long shaft for leverage and a straight end. Production requires the forging and heat treatment of steel. This is challenging and takes time to perfect.
Hultafors has spent a great deal of time and effort in mastering the process. It produces well over 100,000 wrecking bars each year in a range of sizes, including an adjustable wrecking bar. Most of them are distributed to the Nordic countries with a developing footprint in the rest of Europe.
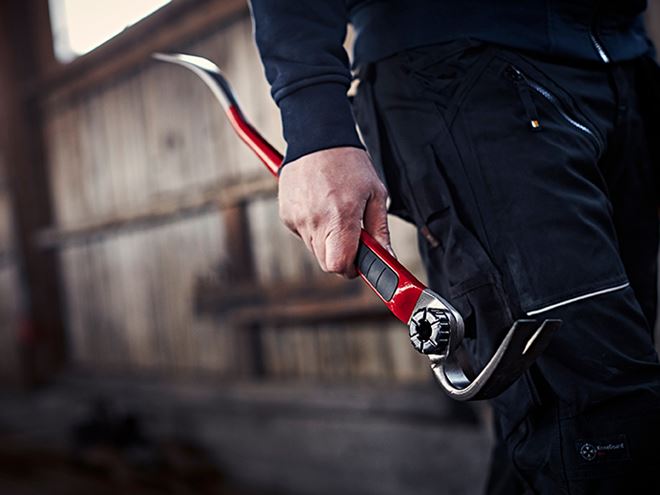
As a company that places a premium on quality and end-user safety, Hultafors has been using our high-alloy boron steel for the past 25 years to manufacture its wrecking bars. Lennart Jansson, Product Manager at Hultafors, says: “The claw of our wrecking bars is the thinnest on the market to enable easy access to narrow spaces." But because of boron steel’s ultra-high strength and durability, it will never break when over-stressed, making it much safer than other bars. It might bend slightly. In contrast, our competitors’ bars have much thicker claws, but can snap without warning, as revealed in our stress-testing program.
In the past we’ve tried other boron steels as well. They appeared to be identical but we weren’t happy with the results. The consistent quality of Ovako’s steel, tight process controls, and good repeatability convinced us to stick with them.
Likewise, Ovako’s technical input has been invaluable, not only for the wrecking bars, but also when we started using another of their steels for our axes, especially regarding material checks, metallurgical investigations, and discussions around material content.”
Why boron steel is ideal for hard-wearing applications
At Ovako, we have pioneered the use of boron steel to help companies like Hultafors produce superior products. Boron is an interstitial element that is added in small amounts to steel to replace expensive alloying additions. It gives the steel a stable, predictable behavior during heat treatment.
Boron steel grades can be hardened either by heat treatment after workshop processing or by a direct hot forming and quenching process to achieve a high-strength component. Even when quenched in water, there is minimal distortion, which reduces the amount of grinding required to the final dimension. The beauty of our boron steel is that customers can easily shape our hot-rolled round and flat bar to their needs and then double the hardness when it is later quenched and tempered.
Sustainable production
The hot-rolled bar steel is covered by an Environmental Product Declaration (EPD). This makes it easier to calculate the cradle-to-gate carbon footprint for all products that contain our boron steel. The EPD is externally verified and proves that each tonne of hot-rolled bar at our Smedjebacken and Boxholm mills in Sweden carries an average footprint, including all upstream sources, of just 389 kg of CO2 equivalent per tonne of finished product, less than 1/6th the global average. We’ve expanded this by launching a Carbon Footprint Calculator to help all our customers develop their own carbon footprint for each specific alloy and product shape combination.
Hultafors shares our commitment for sustainability Lennart Jansson explains “At Hultafors we believe that quality and sustainability go hand in hand and we really appreciate to have a supplier that can deliver on both. That means that we can produce the best wrecking bars in the world without having to compromise with either performance or the environment – and that is exactly how we want to operate.”
The last word on wrecking bars
Lennart Jansson concludes: “Many companies have tried to copy our wrecking bars but without success. We believe Ovako’s superior boron steel, together with the hardening method, gives us the edge. That is why we are now also using the same boron steel grade for the pinch points of our aluminum pry bars."
Read more about Hultafors (website in Swedish)