A visionary and pioneer Berndt Grönblom founded the Elektrometallurgiska Aktiebolaget metal refinery in 1915 in the Vuoksenniska area, producing pig iron and ferrosilicon by smelting scrap metal. The factory initially employed 150 workers.
Grönblom's vision was to ensure Finland's self-sufficiency in the production of iron and steel. Imatra was an excellent location for the new steel mill, as the Imatra rapids provided enough electricity for the process, and raw materials were available nearby. Grönblom laid the solid foundation for the production of special steels in its current form.
The Imatra steel mill is the largest metal industry company in Southeastern Finland and one of the most significant industrial employers in the South Karelia region.
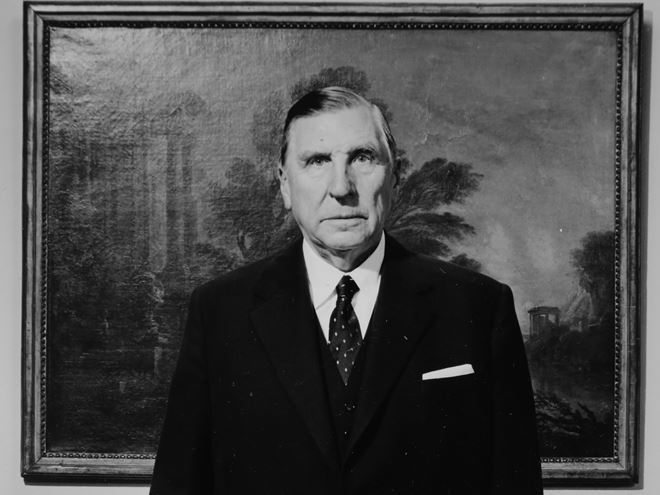
Development begins
After World War I, in 1918, Grönblom continued his determined development of iron refining, but progress was slow, as the Vuoksenniska smelter needed more electrical power, which was only available in 1925—still insufficient for Grönblom's ambitious plans.
In 1926, Grönblom founded the Osakeyhtiö Vuoksenniska Aktiebolaget, establishing a pulp mill next to the smelter so that the limited electricity supply could be used optimally.
In 1928, Elektrometallurgiska Aktiebolaget made an electricity supply agreement with Imatran Voima, which helped accelerate the construction of a new power plant in the Vuoksi valley.
Finally, in 1929, the state-owned power plant opened new possibilities for the wider development of electrometallurgical processes. Over the next few years, the smelter was significantly expanded, and the demand for steel grew along with Finland's industrialization.
In 1933, Elektrometallurgiska Aktiebolaget and Osakeyhtiö Vuoksenniska Aktiebolaget merged to form Oy Vuoksenniska Ab.
The current mill began in phases
In 1935, construction of the Imatra ironworks began at its current location, and production gradually began in 1936-1937. The official inauguration of the new mill took place on June 1, 1938.
In its early years, the ironworks sourced its raw materials from the nearby Outokumpu Ltd. copper plant in Imatra. The byproduct of the copper plant, the so-called "kiisutuhka" (copper slag), was used in the production of pig iron. This was technically challenging, but Grönblom's multi-year research and development project made it possible.
The iron mills' first 25-ton electric arc furnace, with a power capacity of 12,000 kW, was one of the largest in the world. It could produce about 30,000 tons of crude steel annually. A second similar furnace was installed at the mill in 1939.
The refining value of the mills production was further increased by the completion of a heavy bar mill in November 1937. In the early years, the production of the ironworks focused on rails and various railway construction materials for the Finnish state railways.
The Imatra mill was designed from the outset to be an electric steel mill, which is why the steel from Imatra still today has a carbon footprint that is 80% smaller than the global average.
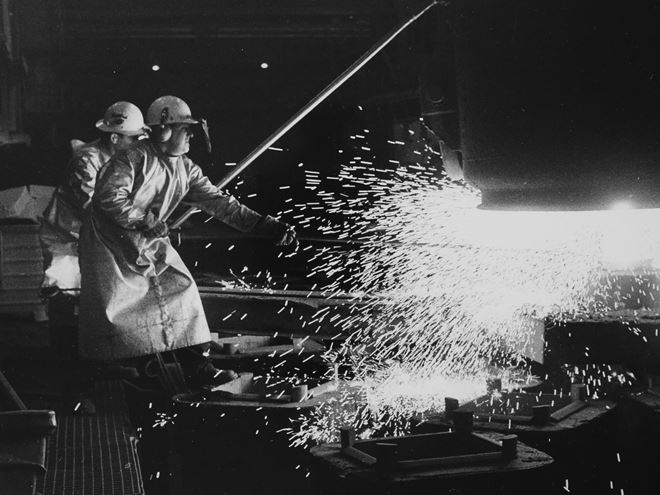
The factory survives the war years
During the Second World War, from 1939-1944, the Imatra mill was almost exclusively dedicated to fulfilling the steel needs of Finland's defense industry. In 1943, operations expanded when the mill's medium and fine bar section mills were commissioned, although construction was delayed or sometimes halted due to the war.
The factory was damaged several times during the Continuation War bombings but was able to continue its operations. The mill remained on Finland's side of the border by a narrow margin—only a couple of kilometers.
The post-war period saw years of growth and investment. The mill's production capacity was increased, as the war reparations to the Soviet Union required an increase in Finland's total steel production capacity.
In the 1960s, the mill expanded its export markets, and the production of special steels grew rapidly. In 1964-65, the largest investment program since the founding years was implemented at the mill.
The mid-1960s were expected to bring an economic upswing, but it did not materialize, and the structural changes in the European steel industry began to impact the Imatra mill's operations. The old units had to adopt new organizational structures, and in 1969, leading Finnish special steel companies Vuoksenniska, Koverhar Oy, and Åminnefors merged to form Ovako, with Wärtsilä becoming a shareholder in 1972.
The threat of closure and a new rise
In the 1970s and 1980s, the profitability of the Imatra mill was improved through significant investments in new technology. In 1986, the Finnish-Swedish corporation Ovako Steel was formed through the merger of the Finnish Ovako and Swedish SKF Steel.
In 1990, Ovako's product sales plummeted along with Finland's general economic situation, and the financial burdens of the ongoing modernization and expansion program began to weigh heavily on the mill.
In early May 1991, Ovako announced that the entire Imatra mill would be shut down. However, the closure was avoided when the managers of the mill managed to save it with the help of Wärtsilä and support from the Finnish government. The Ovako Group was split, and Ovako became Swedish-owned. A new company, Imatra Steel Oy Ab, was established for the Finnish mill.
The government's support was conditional on investments in a new electric furnace and flue gas treatment. Therefore, during the Imatra Steel era, a new 80-ton electric arc furnace and a flue gas purification plant were built at the mill. At the same time, determined work began to reduce emissions.
Owner of the fifth largest steel giant in the world
In 2005, the Imatra mill became part of the new Ovako Group, and today it still operates under the Ovako banner. In September 2010, Ovako was acquired by the investment company Triton. Since 2019, the Ovako Group has been a subsidiary of Japanese Sanyo Special Steel and a member of the Nippon Steel Corporation group. Nippon Steel is the fifth-largest steel producer in the world.
The Imatra steel mill is the largest metal industry company in Southeastern Finland and one of the most significant industrial employers in the South Karelia region. The mill employs about 500 people, and its annual production capacity is 200,000 tons. Around 80% of production is exported.
Since its founding years, the mill has been a pioneer in its field—and it continues to be so today. Together we create steel for a sustainable society.
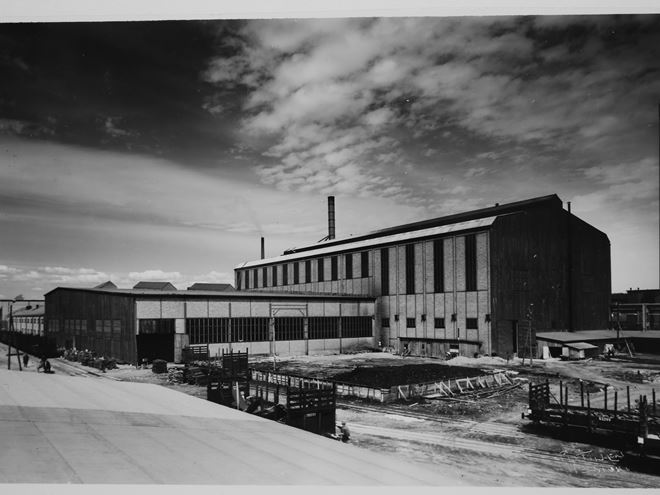
