Steve Ooi is an Ovako Group R&D technical specialist based in England, at the University of Cambridge’s prestigious Maxwell Centre. We asked him to tell us about his background and to answer some questions about the particular benefits of Hybrid Steel.
Steve, what is your role at Ovako?
My particular expertise is on hydrogen in steel and solid phase transformations. I joined Ovako just over a year ago, and I am responsible for various internal and external research projects related to the development of Hybrid Steel. I am also involved in the development of our Sub-Zero steel brand.
What did you do before Ovako?
I obtained my first degree, masters and doctorate from the University of Swansea in Wales. Then I worked at the University of Cambridge for nine years before I joined Ovako. My research was focused on alloy and process design for critical components in aeroengines, automobiles, deep ocean structures and bearings.
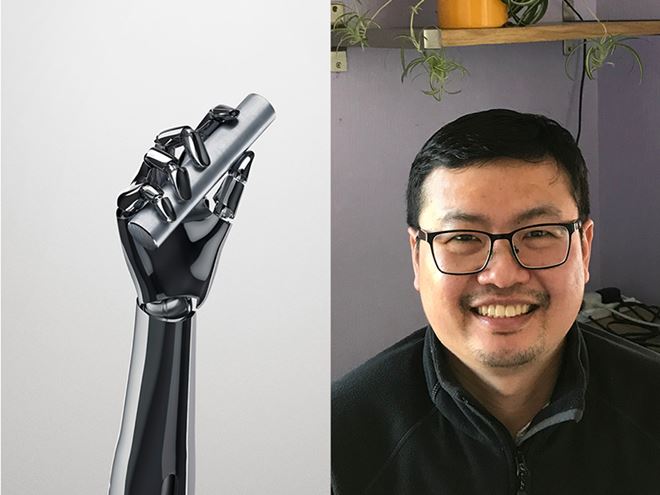
What is Hybrid Steel?
Hybrid Steel is a new steel grade developed by Ovako. It is a secondary hardening steel that combines alloy carbide and intermetallic precipitation hardening. It is cost-effective to produce, corrosion resistant and has high strength at high temperatures. Hybrid Steel has the potential to solve a wide range of industrial challenges, improve production efficiency and save costs.
How does Hybrid Steel achieve its special properties?
The effect of adding alloying elements to the steel microstructure to improve mechanical properties and corrosion resistance has been known for many years. It is though the combination of properties and producibility of Hybrid Steel that make this grade unique. If you look at its chemical composition, you can see that all of the added elements have at least two roles in improving its properties. For example:
- The carbon level is controlled for weldability and carbide formation.
- Chromium is added to improve stability of the passive layer and carbide formation.
- Nickel is added for nickel aluminide precipitate formation and to improve toughness.
- Aluminum is added for nickel aluminide precipitate formation, to increase the martensitic transformation temperature and to reduce density.
And all the added elements increase the hardenability, which ensures an homogeneous microstructure.
How does Hybrid Steel offer high strength at elevated temperatures?
The formation of both chromium carbide and nickel aluminide precipitates that are stable at high temperatures help prevent the movement of dislocations. And in simple terms, when dislocation movements are restricted then steel becomes stronger.
Why does Hybrid Steel enable high-volume, cost-efficient production?
Hybrid Steel is cost-efficient because it is a ‘clean’ ultra high strength steel produced without a secondary re-melting process. Furthermore, it develops its full properties after tempering, which could enable manufacturers to eliminate some of their production steps.
Why does the high hardenability of Hybrid Steel enable low distortion?
Distortion is caused typically by uneven cooling between the surface and the core of a component during quenching. The high hardenability of Hybrid Steel enables parts to be air-cooled, or even furnace cooled. This ensures uniform cooling and hence minimizes distortion.
How does the high cleanness contribute to improved fatigue strength?
High cleanness in steel means that it has a minimum amount of non-metallic inclusions. This reduces the possibility for stress concentration that results in crack formation, and hence improves fatigue strength. In addition to high cleanness, Hybrid Steel also has high microstructural stability that is a further contributing factor in improving fatigue strength.
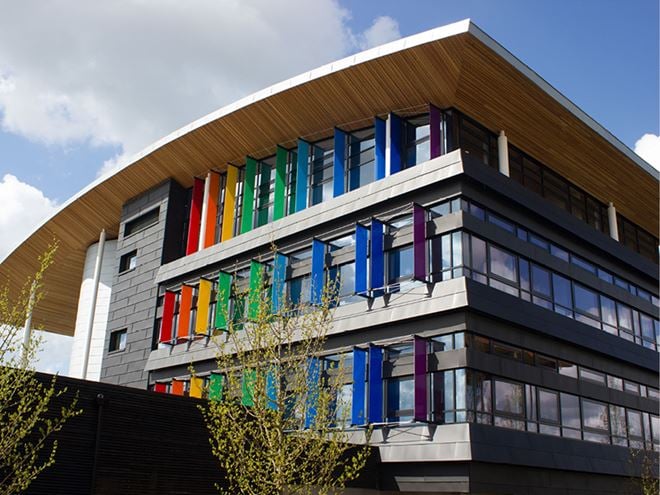
Maxwell Centre at University of Cambridge, England.
How does the low microstructural segregation contribute to the uniform properties of Hybrid Steel?
The low chemical segregation produces a uniform microstructure that results in uniform properties.
Why does Hybrid Steel offer good weldability?
Medium and high carbon steel is difficult to weld, because the formation of brittle martensite following rapid cooling of the weld metal can result in cracking. Hybrid Steel has a low carbon content. This produces softer and more ductile martensite, which does not lead to cracking even after rapid cooling.
What are the surface treatment possibilities for Hybrid Steel?
Possible surface treatments for Hybrid Steel include nitriding, passivation and black oxide coating.
What is special about Hybrid Steel’s corrosion resistance?
Alloying elements in Hybrid Steel such as chromium and aluminium promote the formation of a thin, stable and adherent oxide layer that provides good corrosion resistance.
What are the main applications for Hybrid Steel?
Hybrid Steel offers superior strength over conventional steels, especially for high-temperature applications. Therefore, it has particular appeal for use in engine components, bearings, and tools that operate in extreme environments and in demanding conditions.
Technical Report: Hybrid Steel® - the next step in steel evolution