The traditional approach for the forging industry is to use reheating, quenching, and tempering stages as shown in Figure 1 to attain the ideal steel microstructure in steel components. The aim with quenched and tempered (Q&T) steel is to achieve the optimal balance of strength, ductility, and impact toughness. But what if the required properties could be achieved without these additional stages? Now they can, thanks to the results of Ovako’s extensive research program to create a new generation of direct-quenching steels as illustrated in Figure 2
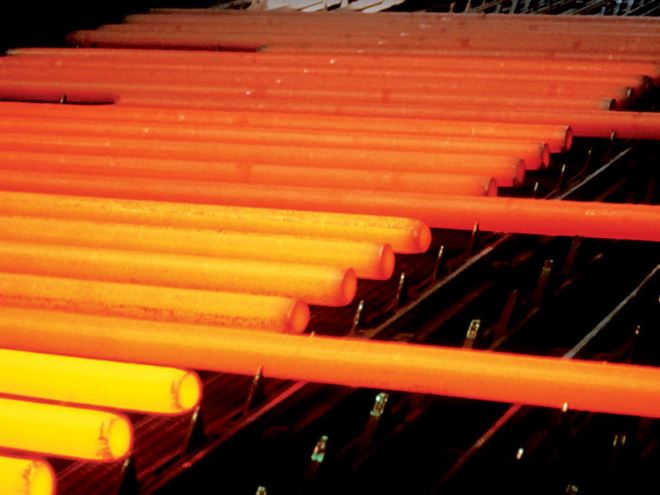
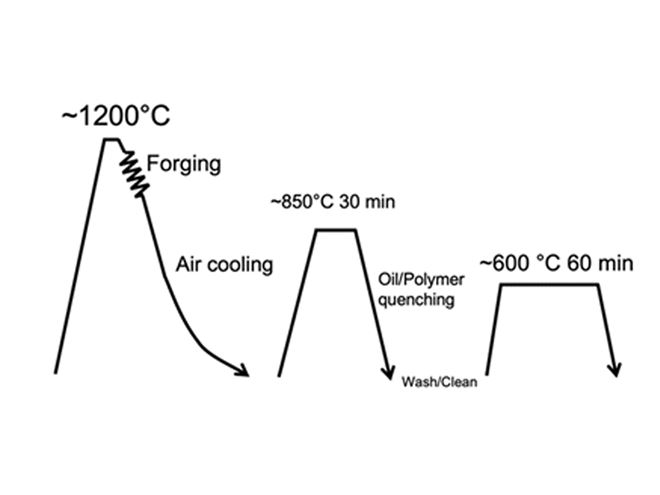
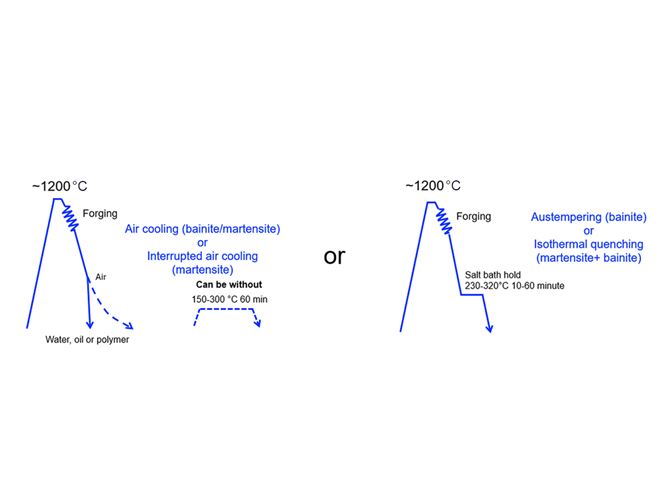
A key factor that has driven Ovako’s interest in this area is that according to Roland Berger's 2022 analysis, we have achieved the world’s lowest Scope 1 and 2 CO₂e emissions (0.09 tCO₂ per ton of steel produced) in the steel industry. And we have also set an ambitious 80% reduction target by 2030. Building on these achievements, we have now turned our focus to pioneering direct-quenching forging steel to help our customers further cut CO₂ emissions by eliminating the energy-intensive reheating process, which also increases productivity.
A further significant advantage of direct-quenching forging is that the elimination of subsequent heat treatment also reduces labor and maintenance costs on existing equipment, as well as the need for capital investment when building a new forging plant.
What difference can direct-quenching steel make to carbon emissions?
Because the traditional Q&T route requires two additional energy-intensive heat treatment steps after forging, this adds cost and complexity to production while generating significant CO₂ emissions from fuel combustion. The advantages of adopting the direct-quenching route become apparent when calculating the CO₂ emissions avoided by eliminating the Q&T process. We estimate the energy requirement for Q&T heat treatment using natural gas to be approximately 700 kilowatt-hours (kWh) per tonne. There are two primary sources for data on CO₂ conversion using natural gas for heating, both yielding relatively similar results:
- 18 kg CO2e/kWh (DEFRA) (Scope 1)
- ~0.2 kg CO2e/kWh ETS (EU Emission Trading System) (Scope 1)
Based on the above conversion, it is estimated that the potential savings using direct-quenching steel are in the region of 126-140 kg CO2e/t for the forged component produced.
New alloy design criteria
The desire for direct-quenching forging steel is not actually new. But this approach has often faced challenges related to meeting toughness requirements at specified strength levels. Historically, to enhance toughness, the microstructure of direct-quenching forging steels has evolved from micro-alloy precipitation-strengthened ferrite-pearlite to upper bainite microstructures. While there have been successful cases using both microstructure types at low strength, many components with a higher demand for strength and toughness still need to be produced using conventional Q&T martensitic steel via energy-intensive processing routes.
What our research has focused on is applying new alloy design criteria together with innovative processing to increase both the strength and toughness of the as-forged component. This allows customers in the forging industry to optimize their use of steel through reduced product size and/or decreased component weight.
The alloy design criteria we employ are focused on the steel’s carbon content for strength and toughness, and its transformation temperature during cooling to achieve the desired microstructure based on the component size and available cooling methods.
The result of the research program is that Ovako is now able to introduce two innovative direct-quenching steel concepts that do not require costly alloying:
- The first achieves high yield strength and Charpy toughness through interrupted water cooling, which is ideal for components up to 80 mm thick. This grade features a controlled transformation temperature of low-carbon martensitic steel, which can be tempered at low temperatures depending on the application. A direct air-cooling steel variant is available, but a higher alloying addition is needed to improve the hardenability.
- The second grade, with medium carbon content and lower alloying content, attains an even greater strength with satisfactory Charpy toughness at room temperature produced via isothermal quenching in a well-agitated salt bath.