French industrial manufacturer BSA Groupe has boosted its efficiency by switching to Ovako’s SP-Bar as a raw material for peeled bar. BSA processes steel products and other alloys for manufacturers in the automotive, pharmaceutical, construction, aerospace, nuclear and defense industries.
Its workshop in Vougy, south eastern France, carries out cold-forming processes such as peeling, grinding, cutting, chamfering, blanking and marking on specialty steel bar. This enables its customers to focus on their own high-value production steps.
“Peeling has the goal of removing imperfections and oxides from the surface of steel bar. We have three peeling lines and process around 18,000 tons of bar per year in diameters from 8 to 100 mm. The process provides a flawless surface so that machine builders and OEMs can build high precision into their equipment,” says Victor Asensio, CEO and owner of BSA Groupe.
“We started using SP-Bar in 2019 because of its unusually tight dimensional tolerances and near-perfect roundness. Because there is minimal variation in the bar’s diameter, we have been able to reduce waste and improve our production yield.”
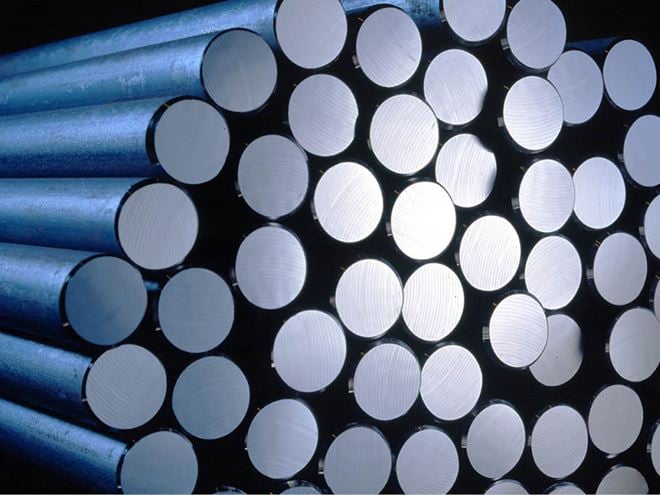
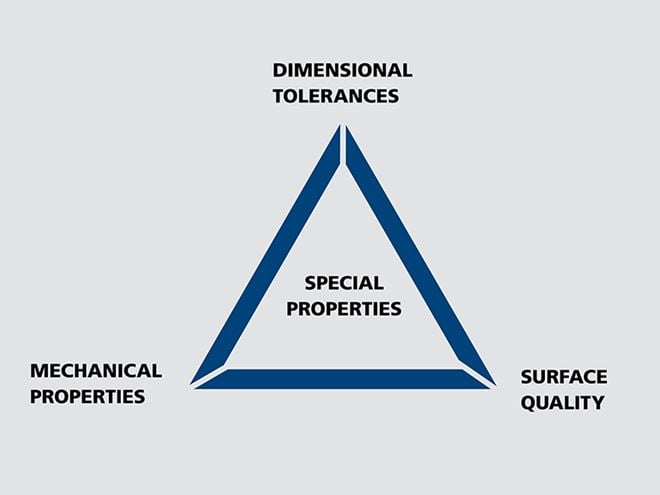
Three special properties
SP-Bar is named because it has special properties in three areas. These are: dimensional tolerances, mechanical performance and surface finish.
“You can get a broad range of characteristics when rolling steel and that might mean variations in mechanical properties, dimensions, surface finish and response to heat treatment,” says Gregory Navarre, Ovako’s General Sales Manager for France. “Careful control in the rolling mill enables us to make steel with defined and stable properties. For OEMs, this means less wastage, less downtime and fewer interruptions to production. It can also improve mechanical performance during a product’s lifetime.”
In the case of tighter tolerances, consistency provides the advantages of improved yield and material savings, stable performance in forming operations and less waste.
Consistent mechanical properties such as toughness and hardenability will increase fatigue life and impact strength.
Finally, consistently good surface quality means less scale and less need for finishing. This results in process savings from having cleaner quenching tanks and an improved production environment.
Precision rolling mill
The key to SP-Bar is the fine-section rolling mill at Ovako’s mill in Boxholm, which carries out finishing rolling on steel bar at closely controlled temperatures, while it is in the austenitic phase.
This ensures the bar will keep its dimensions. However, it also enables finer grain sizes and therefore tougher steel without the build-up of residual stress experienced during cold-rolling. Finally, it also reduces decarburization, meaning less scale.
The fully-automated facility has dedicated rolling stands for roughing, as well as shaping and finishing that provide multiple routes to deliver bar of 14-52 mm diameter. Inter-stand water cooling stations create consistent end-to-end temperatures for each bar and billet in a process that precisely controls the temperature of the steel without quenching it. Cutting shears and in-line measurement gauges provide dimensional control.
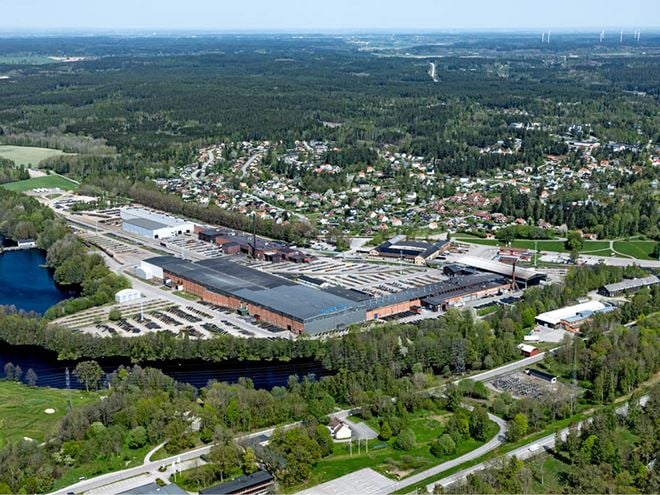
Navarre adds: “Our Boxholm mill developed the SP-Bar technique in 2003 for a customer that wanted bar with a very tight tolerance for roundness. This was not possible at the time as higher rolling temperatures made the bar too soft to maintain perfect roundness. Therefore, our experts at the plant installed cooling stations that use water tubes for better control of rolling temperatures.”
“Since then, they have developed the process even further to reduce decarburization and surface scale. This reduces waste during cold forming and provides a smoother surface finish. We can also use the SP-Bar process to create bar with small grain size, giving it good toughness and a consistent response to heat treatment, which helps to achieve the required hardness.”
The SP-Bar process produces similar results to Kocks rolling, which applies rolling pressure from three axes to control tolerances and roundness. However, order sizes for Kocks blocks rolling are typically at least 200 tonnes. In comparison, we can produce SP-Bar in batches of as little as 12 tonnes, as well as providing the additional benefits of consistency over surface quality and mechanical properties.
High and low alloyed grades
The SP-Bar technique can be used on low alloyed steel to improve production efficiency. It can also enhance the mechanical performance of high alloyed grades, giving superior impact strength, toughness and hardenability.
This makes it suitable for high-performance products where safety is critical such as fasteners for wind turbines.
Tatu Rasanen, Process Development Manager, says: “About one third of our SP-Bar is based on microalloyed grades. The beauty of carrying out finishing rolling in the austenitic phase is that it gives us better control over the precipitation of alloying elements such as vanadium, titanium, niobium, nitrides and carbides. The result is that we can produce steels with a very fine grain size and excellent mechanical properties.
“It’s quite different to thermomechanical rolling, where you carry out rolling below 800 ˚C and then cool the bar after the last rolling stand. In the SP-Bar process, we control the rolling temperature at every stage, with cooling between the stands and a very defined final rolling temperature.
“We are capable of achieving a grain size of 12, which is the finest possible as measured under ASTM International’s measure of the number of grains per square inch at 100x magnification.”
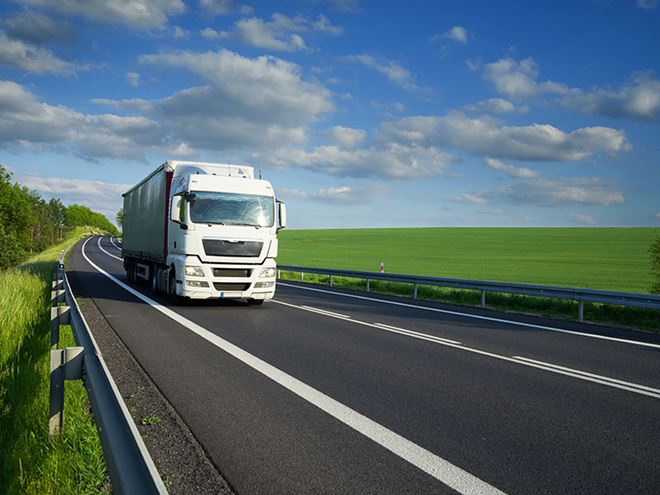
Automotive advantages
Customers in the automotive industry are finding value from the special properties.
For example, one manufacturer is making automotive steering racks based on SP-Bar made from a microalloyed to achieve repeatable mechanical properties, with a secondary benefit being good yield. Elsewhere, SP-Bar’s small grain size has enabled a producer of stabilizer bars to achieve better mechanical properties following heat treatment of a chromium spring steel.
Yet another manufacturer is using SP-Bar made from low-alloyed steel grades to reduce waste during machining thanks to its tight tolerances.
Value of consistency
Ultimately, the SP-Bar process has potential to save material, improve yield, eliminate processing steps, reduce production downtime and setup time, and improve the mechanical performance of end products.
However, its benefits are specific to individual customers and applications. That’s because it provides a bespoke balance between the three characteristics of dimensional tolerances, surface finish and mechanical properties.
“The concept of SP-Bar is straightforward, although it requires in-depth process knowledge and a suitable production line,” concludes Rasanen.
“SP-Bar has huge potential for OEMs that use steel bar as a raw material. However, customers derive value from their own individual balance of the special properties. Therefore, it’s hard to fully understand its potential value until we’ve met with a customer and explored what is possible.”
“One thing helps them overcome their reservations is that they don’t need to make a big commitment as our minimum order quantity of only 12 tonnes. Therefore, customers can try out SP-Bar without committing to a large production run.”
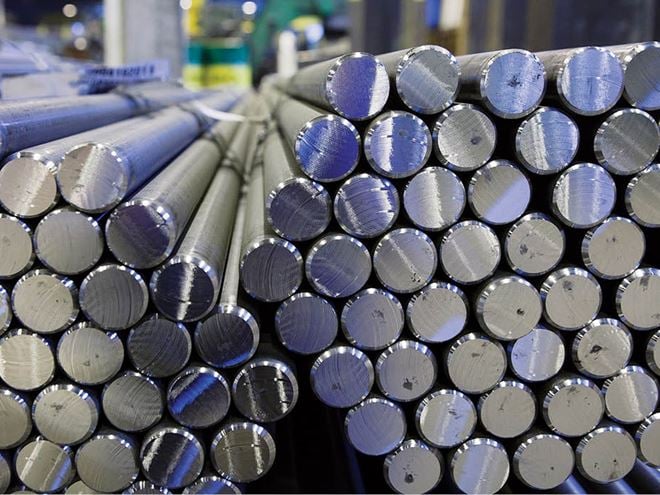