Axes have been used for millennia to shape, cut and split wood, to hunt animals, and as a weapon. Today, they are most commonly used in outdoor pursuits like camping – throwing axes is also a growing recreational activity. But regardless of their intended use, axes must be strong enough to withstand the impact of striking wood and other materials. That’s why Swedish hand tool maker Hultafors uses a custom grade of Ovako steel so that their axes achieve the perfect balance of sharpness, durability, and toughness.
Axe production involves the careful forging and heat treatment of the steel head. Achieving this precision is challenging and takes time to master. What makes Hultafors unique is that it’s one of the few producers that still hand forges their axe heads at Hults Bruk in the Swedish province of Östergötland.
During the coronavirus pandemic, Hultafors’ production peaked at around 180,000 axes because of heightened interest in outdoor activities. Today, most of their customers are hobbyists, campers, and outdoor adventurers. But they still provide tools for professionals, like lumberjacks and woodworkers, in places like Papua New Guinea, Australia, and Canada.
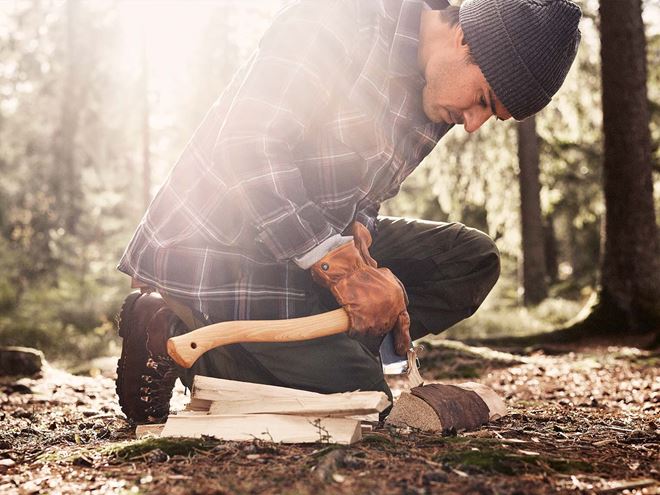
Hultafors has a rich history
Even though Hults bruk has been around since 1697, they didn’t start making axes right away. At first, they made ship nails and later created all sorts of other products, like metal castings. It wasn’t until 1880 that they began producing axes. This change happened when the owner of Hults Bruk at the time, Gunnar Ekelund, thought about what they should focus on to keep the business running smoothly. He decided it was time to focus on making axes more efficiently.
“We aren’t entirely sure why axes became the primary product, but since then, we’ve continuously produced them,” says Lennart Jansson, Product Manager at Hultafors. “Our ownership changed in 1944 when Hults bruk was bought by Holmen, a company interested in the surrounding forest land. They ran the axe factory until 1988, when it was acquired by Hasselfors, who saw the potential for worldwide distribution.”
Anyone shopping for axes online will probably come across two brand names: Hultafors and Hults Bruk. They’re very much the same axes, just with different names. In the US, the old name ‘Hults Bruk’ is still used, while in Europe, they go by ‘Hultafors.’ This is because Hults Bruk joined the Hultafors group back in 1992.
Valuing craftsmanship and precision
Hultafors’ axe heads are forged from a custom grade of Ovako forging steel of a consistently high quality. The production process starts with flat steel bars of different sizes. These bars are cut to the right length for each axe model, then shaped using traditional forging.
Jansson explains: “Forging is a unique and historical part of our production process, virtually unchanged since 1880. We use machines from the 1950s and 1960s and perform free-form forging in open dies. This method contrasts with faster, drop-forging techniques from our competitors, where only three to four strikes are needed to craft a head.”
The forging requires about 40 to 60 strokes to shape the material precisely. That’s why Hultafors finds blacksmithing expertise very important. “Our forging process preserves historical craftsmanship, making every axe unique,” Jansson adds. “Each piece has small variations, even though they meet standardized specifications. This traditional method is also a major selling point.”
But not everyone can be a highly skilled blacksmith. This makes it challenging to recruit and train new talent – it can take anywhere from one to three months to learn the basics and up to a year to become proficient. Jansson says that qualities like good hand-eye coordination (found in a lot of dancers or athletes) are helpful to become a blacksmith.
Currently, Hultafors employs around 10 blacksmiths. But they plan to increase that number while maintaining safe routines for workers to prevent fatigue or injuries.
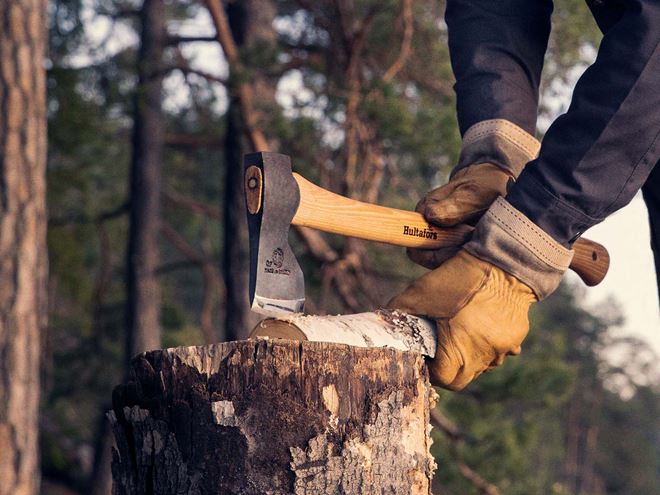
Why hardening steel is ideal for axe applications
At Ovako, we have helped companies like Hultafors produce superior products through our high-performance steel. Thanks to a closely controlled production chain from initial melt to final delivery, our steel is known for its highly stable material quality with narrow process parameters.
After forging the axe head, Hultafors' blacksmiths carry out several steps to finish the surface, like heating, grinding, hardening, tempering, and polishing. Using high-quality steel can make this process more efficient by improving the axe’s durability and making the material easier to work with. Plus, our steel helps their axes last longer and reduces their environmental impact by cutting the carbon footprint by 80 percent.
Benefits also include longevity and a vintage appeal
Ovako steel is strong, tough, and resistant to wear and damage, making it ideal for axes that must handle repeated impact with materials like wood. The steel is also recyclable and tough enough to handle heat and heavy use, making it long-lasting.
The longevity of Hultafors’ products has created a thriving secondary market for their vintage axes. “Enthusiasts love restoring old pieces, replacing the handles, and polishing the heads,” Jansson explains. “On our website, there’s even a section dedicated to vintage axes where collectors discuss models, stamps, and authentication details.”
The last word on high-quality axes
Jansson concludes: “True quality comes from the perfect blend of rich history, traditional craftsmanship, and superior materials — with Ovako steel playing a key role. A Hultafors premium axe, priced between €90 and €200 (around 900 to 2000 SEK), isn’t just a tool – it’s a testament to the skill, care, and dedication poured into every piece.”
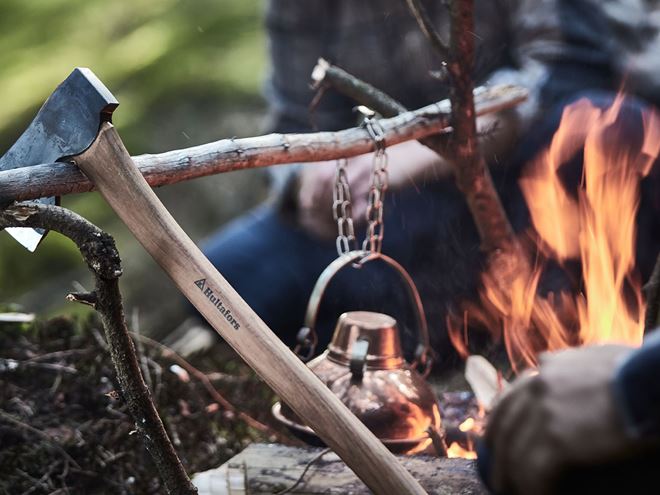