Quenching and tempering process for high-strength fine-grained steel
Quenching and tempering remain cornerstone techniques in modern steel production, delivering reliable and versatile solutions for industries that demand high-performance materials. Steels treated through this process provide a unique combination of strength, toughness, and durability, making them indispensable for challenging environments.
At Ovako, our expertise in producing steels optimized for quenching and tempering is of a high grade. Whether you need unalloyed or low-alloyed grades, our solutions ensure the highest levels of performance and reliability.
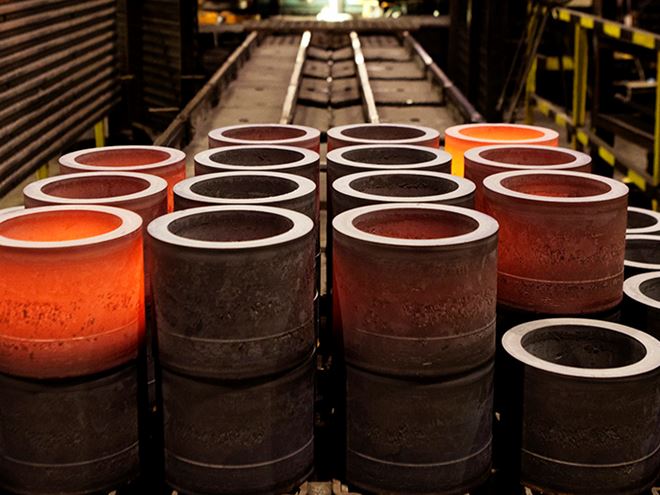
How does quenching and tempering work?
Quenching and tempering is a two-stage heat treatment process designed to optimize steel’s performance:
Quenching (hardening):
- The steel is first heated to its austenitizing temperature, typically around 900°C.
- At this temperature, the steel’s structure transforms into austenite.
- It is then rapidly cooled using water, oil, or another cooling medium, which converts the structure into martensite – a hard, but brittle phase.
Tempering:
- After quenching, the steel is reheated to a lower temperature, usually between 150°C and 700°C, depending on the desired properties.
- This step relieves stresses introduced during quenching, improves toughness, and balances strength with ductility.
- Tempering results in a fine-grained, homogeneous microstructure tailored to meet specific application requirements.
Why quenching and tempering?
This process is used to create steel with superior mechanical properties that are essential for a wide range of applications. Key benefits include:
-
Increased Strength and Toughness: Quenching and tempering produces steel with high tensile strength and excellent resistance to impact.
-
Improved Wear Resistance: Ideal for components subjected to abrasive conditions, such as tools and machine parts.
-
Versatility: By adjusting the tempering process, the mechanical properties can be fine-tuned to meet specific operational needs.
-
Reliability: The process ensures a consistent and high-quality material, suitable for critical applications.
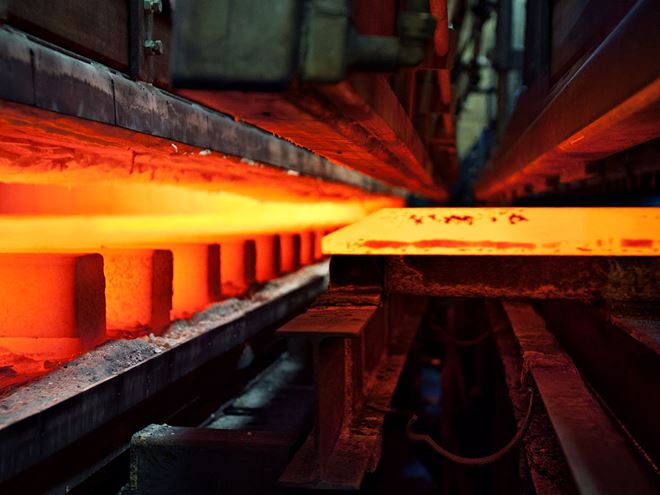
EN-standard |
Ovako |
Typical analysis |
||||||
C |
Si |
Mn |
Cr |
Mo |
Ni |
Other |
||
24CrMo13-6 |
0.24 |
0.2 |
0.4 |
3.1 |
0.5 |
|
|
|
25CrMo4 |
0.25 |
0.2 |
0.9 |
1.1 |
0.2 |
|
|
|
34CrMo4 |
0.34 |
0.3 |
0.8 |
1.1 |
0.2 |
|
V |
|
42CrMo4 |
0.42 |
0.3 |
0.8 |
1.1 |
0.2 |
|
|
|
43CrMnMo4-4 |
0.43 |
0.3 |
0.9 |
1.0 |
0.2 |
|
|
|
44CrMnMo4-4* |
0.44 |
0.3 |
0.9 |
1.0 |
0.2 |
|
|
|
50CrMo4 |
0.51 |
0.2 |
0.7 |
1.0 |
0.2 |
|
|
|
23MnNiMoCr5-4 | 4209 |
0.23 |
0.2 |
1.3 |
0.5 |
0.6 |
1.0 |
|
30CrNiMo8 | 6507 |
0.30 |
0.3 |
0.7 |
2.0 |
2.0 |
0.3 |
|
30NiCrMo16-6 | 498 |
0.30 |
0.3 |
0.5 |
1.4 |
0.2 |
4.0 |
|
31NiCrMo13-4* | 453 |
0.31 |
0.2 |
0.5 |
1.1 |
0.2 |
3.1 |
|
34CrNiMo6 | 356, 6502 |
0.34 |
0.2 |
0.7 |
1.4 |
0.2 |
1.3 |
|
40SiCrMnMo7-6-6* |
477 |
0.40 |
1.7 |
1.5 |
1.5 |
0.4 |
|
|
40CrMoV4-6 | 6098 |
0.40 |
0.3 |
0.7 |
1.1 |
0.6 |
|
V |
21CrMoV5-7* |
0.21 |
0.3 |
0.6 |
1.4 |
0.7 |
|
V |
|
37CrV3* |
9217 |
0.37 |
0.3 |
0.8 |
0.8 |
|
|
V |
40NiCrMo7-3* |
0.40 |
0.3 |
0.7 |
0.8 |
0.3 |
1.8 |
V |
|
32CrMoV12-10* |
0.32 |
0.3 |
0.5 |
3.0 |
1.0 |
|
V |
|
30CrMoV9 |
0.31 |
0.2 |
0.6 |
2.5 |
0.2 |
|
V |
|
40CrMoV4-6* |
0.42 |
0.2 |
0.8 |
1.1 |
0.9 |
4.0 |
V |
|
48CrMoNi4-10* |
0.48 |
0.2 |
0.8 |
1.1 |
0.9 |
4.0 |
V |
|
42NiSiCrMo8-7-3* |
0.42 |
1.6 |
0.6 |
0.7 |
0.3 |
1.7 |
V |
|
4CrMn16-4* |
0.04 |
0.3 |
1.0 |
4.0 |
|
|
Nb |
|
7CrMoBS4* |
0.07 |
0.3 |
0.8 |
1.3 |
|
|
B |
|
8CrMnMo15-4* |
0.08 |
0.3 |
1.0 |
4.0 |
0.5 |
|
|
EN-standard designation followed by “*” is not an official EN standard grade but named according to the rules in EN 10027.
Steel Navigator - Find the right steel for your application
Steel Navigator contains a selection of useful tools such as Material Data Sheets, Machining Calculator, Heat Treatment Guide, Piston Rod Predictor and more.
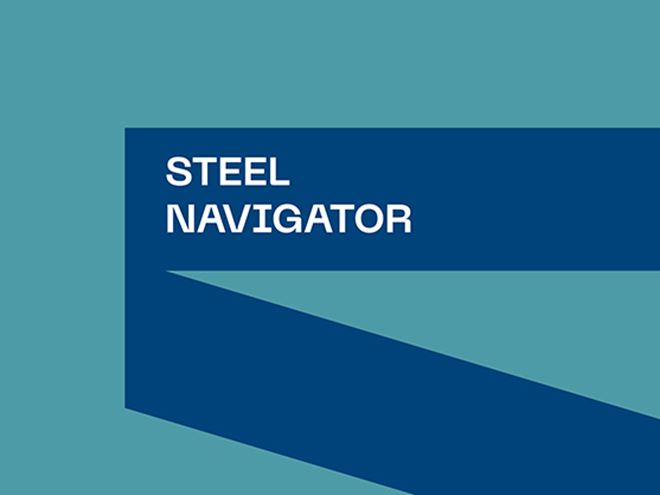