Efficient Processes
Ovako’s production is based on 97 % steel scrap, making Ovako the biggest scrap recycler in the Nordics. Since steel can be recycled an infinite number of times without its properties deteriorating, Ovako can manufacture steel with a lower climate impact without compromising the quality. This is one of the reasons why Ovako products have an 80 % lower carbon footprint "cradle-to-gate" compared to the global average.
Ovako is steadily improving its environmental impact through ongoing development of its production processes. The company constantly strives to reduce emissions from its product manufacturing. All production units are ISO 14001 certified.
Ovako has published Environmental Product Declarations (EPD) that cover the full environmental impact of hot-rolled steel bars from Ovako’s Hofors, Imatra, and Smedjebacken and Boxholm (Smebox) mills.
Here you can download Ovako´s EPDs.
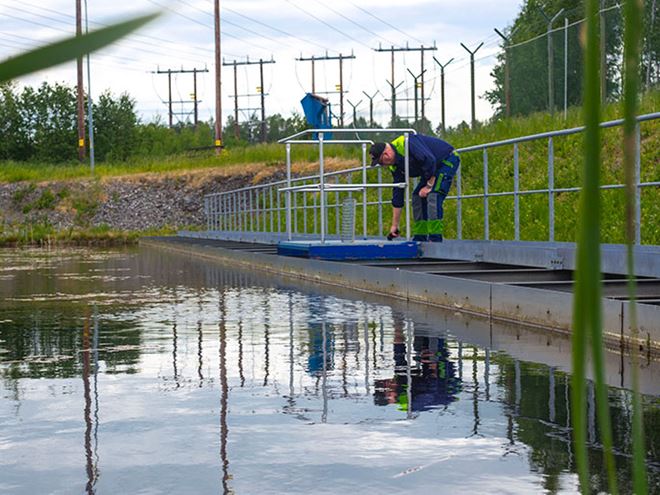
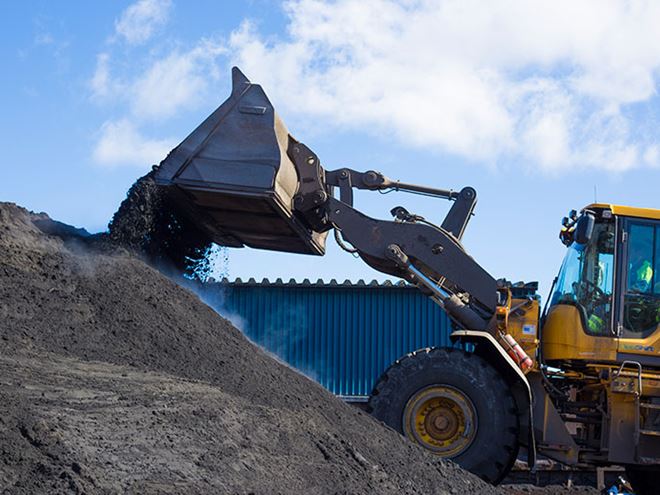
Examples of improvements include:
Energy efficienct - Ovako works continuously on improving energy efficiency. All major production units work according to, or are energy-certified under, ISO 50001.
Resource optimization - To optimize usage of the steel’s alloying elements, the scrap is sorted into various quality categories depending on alloy content, size and shape.
Reuse of water - Ovako is working actively to achieve the most efficient possible use of water in production, including circular systems for reusing water, even though all major production sites are located in areas that are not classified as water stressed.
Emissions to air and water - The main emissions to air are carbon dioxide and nitrogen oxides from combustion, and dust from steel mills and mechanical processing. The emissions are reduced through ongoing development of more efficient processes.
Process water is recycled and, before being discharged, it is treated in internal water treatment plants. All emissions are regularly monitored according to self-inspection programs.
Examples of energy efficiency measures
- Conversion of furnaces from LPG and oil to electricity.
- Heat recovery - all major production facilities in Sweden are selling residual heat to local district heating networks.
- Heat from process cooling water is recovered in several locations, which means that net usage of district heating to warm these buildings has essentially been reduced to zero.
Transport optimization - Ovako is conducting ongoing work to reduce the environmental impact from transportation, including the use of a larger proportion of rail freight, increased co-loading and more modern vehicles.
Residual products - Ovako works constantly to identify new applications for the residual products resulting from steel manufacturing. Using by-products, reusing internal materials and recovering metal content can reduce the extraction of virgin raw materials. Of the residual products, our overarching objective is to maintain an average target of 90 % recycling.
Biodiversity - To preserve biodiversity and support unusual plant species, Ovako is, for example, working actively to ensure that the Värnabackarna birch pasture at our Hofors site is grazed by cattle.